Abstract
Owing to the advantages like high specific strength, high heat resistance and excellent wear resistance, carbon fiber reinforced polymers (CFRP) are used widely in the aerospace field. Nevertheless, due to shortcomings such as anisotropy and uneven phase distribution, the cutting failure behavior of CFRP includes a series of complex processes like fiber delamination and matrix fracture, which are thus classified as difficult-to-machine materials. In this study, the models for predicting relationships of cutting force with process parameters and with surface roughness are created by model analysis, in order to explore the effects of process parameters (cutting speed, feed rate and cutting depth) on the cutting force and surface roughness. As the results show, the cutting depth has the greatest influence on the cutting force, and an interaction is present among the process parameters regarding their effects on the magnitude of cutting force. Moreover, the effects of cutting forces in three directions on the roughness are also significantly interactive. Regarding the prediction models, the use of cutting force yields more accurate and stable prediction of roughness than the direct use of process parameters.











Similar content being viewed by others
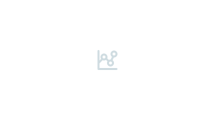
References
Xu WX, Zhang LC (2014) On the mechanics and material removal mechanisms of vibration-assisted cutting of unidirectional fibre-reinforced polymer composites. Int J Mach Tools Manuf 80-81:1–10
Xu WX, Zhang LC (2016) Mechanics of fibre deformation and fracture in vibration-assisted cutting of unidirectional fibre-reinforced polymer composites. Int J Mach Tools Manuf 103:40–52
Niu B, Su YL, Yang R, Jia ZY (2016) Micro-macro-mechanical model and material removal mechanism of machining carbon Fiber reinforced polymer. Int J Mach Tools Manuf 111:43–54
Karpat Y, Polat N (2013) Mechanistic force modeling for milling of carbon fiber reinforced polymers with double helix tools. CIRP Ann 62(1):95–98
Malekian M, Mostofa MG, Park SS, Jun MBG (2012) Modeling of minimum uncut chip thickness in micro machining of aluminum. J Mater Process Technol 212(3):553–559
Afazov SM, Ratchev SM, Segal J (2010) Modelling and simulation of micro-milling cutting forces. J Mater Process Technol 210(15):2154–2162
Maher I, Eltaib MEH, Sarhan AAD, El-Zahry RM (2014) Cutting force-based adaptive neuro-fuzzy approach for accurate surface roughness prediction in end milling operation for intelligent machining. Int J Adv Manuf Technol 76:1459–1467
Ding ZS, Sun GX, Guo XM, Jiang XH, Li BZ, Liang SY (2020) Effect of phase transition on micro-grinding-induced residual stress. Effect of phase transition on micro-grinding-induced residual stress Journal of Materials Processing Technology 281:281. https://doi.org/10.1016/j.jmatprotec.2020.116647
Yang AM, Han Y, Pan YH, Xing HW, Li JZ (2017) Optimum surface roughness prediction for titanium alloy by adopting response surface methodology. Results in Physics 7:1046–1050
Karkalos NE, Galanis NI, Markopoulos AP (2016) Surface roughness prediction for the milling of Ti–6Al–4V ELI alloy with the use of statistical and soft computing techniques. Measurement 90:25–35
Slamani M, Chatelain JF (2019) Kriging versus Bezier and regression methods for modeling and prediction of cutting force and surface roughness during high speed edge trimming of carbon fiber reinforced polymers. Kriging versus Bezier and regression methods for modeling and prediction of cutting force and surface roughness during high speed edge trimming of Carbon fiber reinforced polymers Measurement 152:152. https://doi.org/10.1016/j.measurement.2019.107370
Li C, Li XL, Wu YQ, Zhang FH, Huang H (2019) Deformation mechanism and force modelling of the grinding of YAG single crystals. Int J Mach Tool Manu 143:23–37
Tandon V, El-Mounayri H, Kishawy H (2002) NC end milling optimization using evolutionary computation. Int J Mach Tool Manu 42(5):595–605
Rao RV, Pawar PJ (2010) Parameter optimization of a multi-pass milling process using non-traditional optimization algorithms. Appl Soft Comput 10(2):445–456
Guo WC, WU CJ, Ding ZS, Zhou QZ (2021) Prediction of surface roughness based on a hybrid feature selection method and long short-term memory network in grinding. Int J Adv Manuf Technol 112(9):2853–2871
Wu CJ, Pang JZ, Li BZ, Liang SY (2019) High-speed grinding of HIP-SiC ceramics on transformation of microscopic features. Int J Adv Manuf Technol 102:1913–1921
Sheikh-Ahmad JY, Dhuttargaon M, Cheraghi H (2017) New tool life criterion for delamination free milling of CFRP. Int J Adv Manuf Technol 92:2131–2143
Jia ZY, Su YL, Niu B, Bai Y, Bi GJ (2016) Deterioration of polycrystalline diamond tools in milling of carbon-fiber-reinforced plastic. J Compos Mater 51(16):2277–2290
Wang CY, Ming WW, An QL, Chen M (2016) Machinability characteristics evolution of CFRP in a continuum of fiber orientation angles. Mater Manuf Process 32:1041–1050. https://doi.org/10.1080/10426914.2016.1269915
Zhuang KJ, Zhu DH, Zhang XM, Ding H (2014) Notch wear prediction model in turning of Inconel 718 with ceramic tools considering the influence of work hardened layer. Wear 313(1–2):63–74
Boing D, Castro FL, Schroeter RB (2019) Prediction of PCBN tool life in hard turning process based on the three-dimensional tool wear parameter. Int J Adv Manuf Technol 106:779–790
Chen T, Gao F, Li SY, Liu XL (2018) Experimental study on cutting tool wear in milling carbon fiber composites with spiral staggered diamond-coated milling cutter. Int J Adv Manuf Technol 98(1–4):413–419
Chen T, Xiang JP, Gao F, Liu XL, Liu GJ (2019) Study on cutting performance of diamond-coated rhombic milling cutter in machining carbon fiber composites. Int J Adv Manuf Technol 103(9–12):4731–4737
Lamikiz A, de Lacalle LNL, Sanchez JA, Salgado MA (2004) Cutting force estimation in sculptured surface milling. Int J Mach Tools Manuf 44(14):1511–1526. https://doi.org/10.1016/j.ijmachtools.2004.05.004
da Silva RB, Machado AR, Ezugwu EO, Bonney J, Sales WF (2013) Tool life and wear mechanisms in high speed machining of Ti–6Al–4V alloy with PCD tools under various coolant pressures. J Mater Process Technol 213(8):1459–1464. https://doi.org/10.1016/j.jmatprotec.2013.03.008
Jiang XH, Li BZ, Yang JG, Zuo XY (2013) Effects of tool diameters on the residual stress and distortion induced by milling of thin-walled part. Int J Adv Manuf Technol 68:175–186
Jiang XH, Kong XJ, Zhang ZY, Wu ZP, Ding ZS, Guo MX (2020) Modeling the effects of Undeformed Chip volume (UCV) on residual stresses during the milling of curved thin-walled parts. Int J Mech Sci 167:105162. https://doi.org/10.1016/j.ijmecsci.2019.105162
Zhu DH, Feng XZ, Xu XH, Yang ZY, Li WL, Yan SJ, Ding H (2020) Robotic grinding of complex components: a step towards efficient and intelligent machining – challenges, solutions, and applications. Robot Comput Integr Manuf 65:101908. https://doi.org/10.1016/j.rcim.2019.101908
Lv YJ, Peng Z, Qu C, Zhu DH (2020) An adaptive trajectory planning algorithm for robotic belt grinding of blade leading and trailing edges based on material removal profile model. An adaptive trajectory planning algorithm for robotic belt grinding of blade leading and trailing edges based on material removal profile model Robotics and Computer-Integrated Manufacturing 66:66. https://doi.org/10.1016/j.rcim.2020.101987
Availability of data and materials
The data and materials that support the findings of this study are available from the corresponding author upon reasonable request. All data generated or analyzed during this study are included in this published article.
Funding
This project is supported by Shanghai Science and Technology Commission (Grant No.20ZR1438000) and Innovation Funding of Shanghai Aerospace Science and Technology (Grant No.SAST2019–065).
Author information
Authors and Affiliations
Contributions
Jiang Xiaohui: Conceptualization, Methodology. Gao Shan: Data curation, Validation, Writing- Original draft preparation. Zhang Yong: Visualization, Investigation. He Shirong: Supervision. Liu Lei: Writing- Reviewing and Editing.
Corresponding author
Ethics declarations
Conflict of interest
The authors declare that they have no conflict of interest.
Ethical approval
Compliance with ethical approval.
Consent to participate and publish
The authors agreed to participate and publish.
Additional information
Publisher’s note
Springer Nature remains neutral with regard to jurisdictional claims in published maps and institutional affiliations.
Rights and permissions
About this article
Cite this article
Xiaohui, J., Shan, G., Yong, Z. et al. Prediction modeling of surface roughness in milling of carbon fiber reinforced polymers (CFRP). Int J Adv Manuf Technol 113, 389–405 (2021). https://doi.org/10.1007/s00170-021-06609-2
Received:
Accepted:
Published:
Issue Date:
DOI: https://doi.org/10.1007/s00170-021-06609-2