Hollow Section Fibers Characterization for Seats Covers Fabric Application
- 1Dipartimento di Chimica e NIS Research Centre, University of Turin, Turin, Italy
- 2Group Materials Labs, Polymers Group, Centro Ricerche Fiat, Turin, Italy
This research is focused on hollow polyethylene terephthalate (PET) fibers and fabrics. The aim of hollow section fibers application is a textile contribution to weight reduction of the whole vehicle. CO2 emissions consequences and awareness of companies to environmental issues are driving studies on the direction of vehicle weight reduction, according to recent European regulations. For this purpose, fabrics composed of hollow fibers have been produced and characterized. In order to be applied as seats covers for the automotive sector, they have been compared to current production woven fabrics. Tensile, tear strength tests and aesthetic and structural abrasion have been carried out. The performance of hollow fibers PET fabrics is slightly lower than full section fabrics, but completely acceptable according to automotive requirements. Its specific application can be evaluated.
Introduction
Due to recent European regulations and Companies’ awareness to environmental issues, CO2 emissions need to decrease and more recycled materials need to be used. Recycling involves reducing waste and production of new materials, recovering and transforming of refuse. PET and other plastics affect the amount of waste for disposal, but they can be recycled, as an economical way to reduce plastic waste for automotive application (Cole and Sherman, 1995; Jambor and Beyer, 1997; Koch, 2005). Apart from Companies’ responsibility, Customers’ awareness in reducing fuel consumption and using fuels from renewable resources are important (Official Journal of the European Union, 2009). In fact, CO2 production is directly related to type and fuel consumption quantity. European legislation has set 95 g/km maximum limit of CO2 emission within 2020 (Official Journal of the European Union, 2009; Poyant, 2013).
Carmakers have been looking for new ways for reducing CO2 emissions, focusing on increasing the use of recycled materials and vehicle total weight reduction. The technology of new engines is related to innovation with an increased efficiency, trying to reduce fuel consumption in conventional engines or using renewable resources origin fuels together with new kinds of engines. Emissions reducing is related to whole vehicle weight reduction, and similarly, vehicle weight reduction affects fuel consumption for 75% (Fredriksson and Veitl, 2011; Poyant, 2013).
In the recent years, the average weight of vehicles has been increasing from 800 kg of 1970s to its climax, 1300 kg of 2012. The increase is approximately 32% (Koch, 2005). 100 kg vehicle weight reduction can cause fuel consumption decreasing of 0.3–0.8 L per 100 km (Fredriksson and Veitl, 2011).
In the textile field for automotive application, awareness of environmental issues is related both to the use of green materials from recycled sources and to weight reduction. To continue in the eco-friendly direction for the automotive area, in this work our attention will be driven to the last objective.
A study (Albini et al., 2019), about recycled PET fabrics for automotive application has already proved that post-consumer PET fibers can be used to make yarns and fabrics, which withstand all high technical requirements. Instead, in order to reduce the weight of the whole vehicle, a collaboration among automotive sectors is essential and a contribution of all areas can be decisive. These areas are car body development, engine manufacturing departments and design. The goal of reducing total weight of vehicle can be achieved using lightweight materials (Cole and Sherman, 1995; Jambor and Beyer, 1997). Among these, plastics, composites and light alloys (Lyu and Choi, 2015). Reducing weight in every kind of component affects vehicle final weight (Cole and Sherman, 1995; Jambor and Beyer, 1997). Textile covering also conditions the whole weight of about 20 kg and this could be a significant part if related with all other improvements in weight (Fredriksson and Veitl, 2011). Textile materials cover seats, floor, door panels, ceiling and they are used in functional roles, as for seat belts, pipes, airbags, and tires.
Textile weight reduction is demanding. First, fabrics have to meet automotive requirements to satisfy applications with high technical-mechanical performances. High wear resistance, fastness to light, comfort and safety features are fundamental characteristics to ensure durability of the vehicle (Fung and Hardcastle, 2001; Hearle and Morton, 2008). Different papers tell about possible applications of hollow fibers in the automotive sector. For example, hollow fibers fabrics for interiors insulation applications or composing technical non-woven (Mahmoud et al., 2011; Ki-Young et al., 2013).
The objective of this research is to examine hollow section PET fibers and hollow PET fibers fabric. These fabric properties need to be equivalent to current production fabrics for seats covers application. Hollow fibers are polymeric fibers with a continuous hole running down the middle (Eichhorn et al., 2009). This particular section affects fabric mechanical, structural and after wearing aesthetical final properties (Matsudaira et al., 1993; Khoddami et al., 2009). Hollow fibers fabrics have been compared to current production fabrics in order to evaluate their possible application. Fabrics characteristics and hollow section fibers fabrics final weight reduction will be evaluated. Assessing different mechanical properties, this research can contribute increasing knowledge about hollow fibers production and fabrics characteristics and, above all, their possible applications.
For Original Research Articles, Clinical Trial Articles, and Technology Reports the introduction should be succinct, with no subheadings. For Case Reports the Introduction should include symptoms at presentation, physical exams, and lab results.
Materials and Methods
An Italian manufacturer supplied fibers. PET hollow section fibers and full section fibers were produced. The production of the two different fibers is substantially equivalent in order to obtain two final products comparable. Fibers production starts from PET chips, which are crystallized at 100–170°C before the spinning process, in order to decrease the humidity content. After that, PET chips are melted, extruded and sent to the dosing pumps. They were mass dyed in black. The parameters of the first step of fibers production are:
• Entry air temperature (drying) 170°C; exit air temperature (drying) 100°C;
• Enter temperature (extrusion) 270°C; exit temperature (extrusion) 280°C;
• Rotating pumps speed is 21,6 rpm for hollow ones and 25,7 rpm for full ones;
• Spinneret pack holes number is 56 for hollow ones and 48 for full ones;
• Cooling temperature is 30°C;
• Yarn collecting speed is 3000 m/min for hollow ones and 3050 m/min for full ones;
• Yarn count (for each yarn end) is 235 dtex for hollow ones and 257 dtex for full ones;
• Finish is texturing for both fibers type.
Main differences between hollow and full section fibers production are rotating speed and number of holes of the spinneret pack (Figure 1). Melted material is sent to the spinneret pack, composed of 48 and 56 holes for full and hollow section fibers production, respectively.
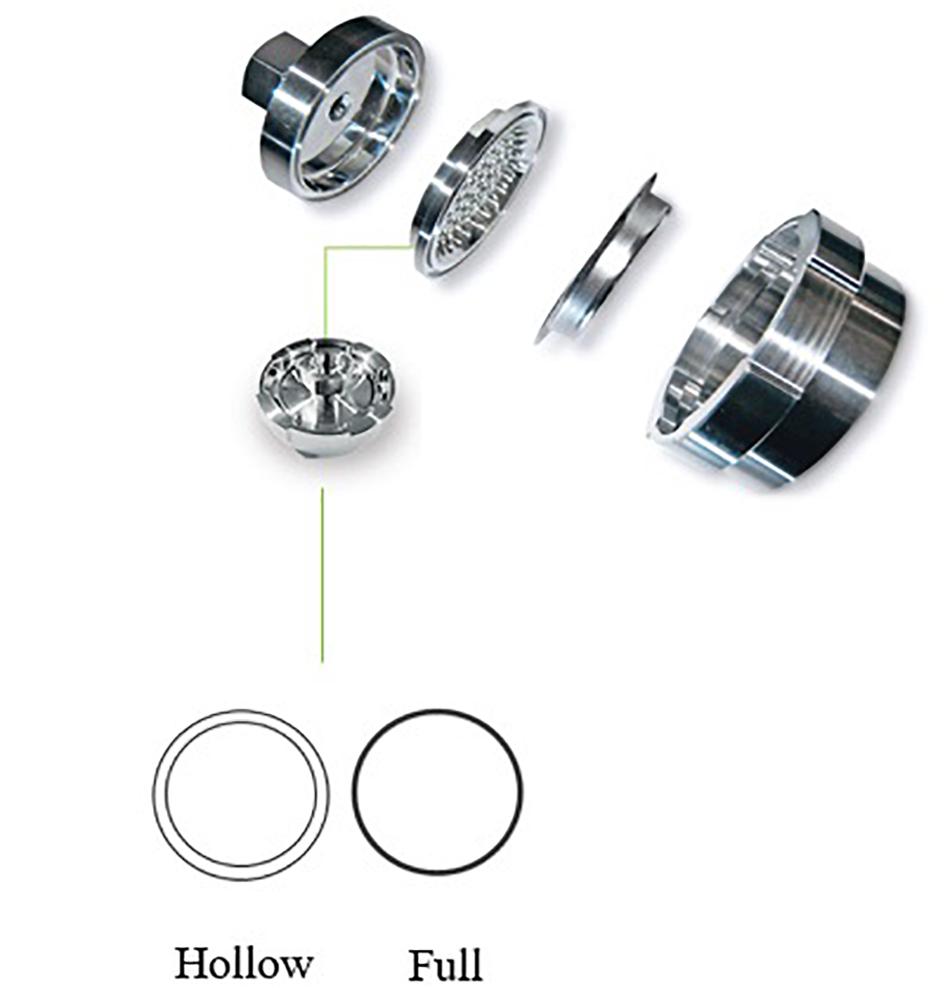
Figure 1. Part of the spinneret pack (Lukay Nonwoven Solutions, 2019) and hollow (left) and full (right) section of spinneret pack holes.
Because of lower covering capability of hollow section fibers yarns compared to full section fibers yarns, the holes number of the spinneret pack has been increased to give them better covering capability and volume and make them comparable to full section fibers.
As regards hollow fibers production, the hole is usually shaped with the introduction of air or other gas (nitrogen) in the polymeric solution (wet spinning process) or melt spinning through specially designed spinnerets. For this research, the method is the last. Hollow fibers provide greater bulk with less weight. Exiting the spinneret pack, yarns are POY (partially oriented yarn) and they progressively are cooled, stretched and textured with “Taslan” process. The last process allows the yarn to be structurally modified with a air flow bending some areas of the yarn and creating curled fibers on the yarn itself, giving the yarn specific characteristics (Andreoli and Freti, 2004).
The two kinds of fiber sections have been structurally analyzed by a metallographic microscope Reichert MeF3A, to understand their section. The preparation of the samples for microscope analysis includes yarns insertion into a thermosetting resin. These samples are 40 mm wide. The upper side of the sample is polished with abradents and diamond paste to better evaluate its surface.
Yarns and fabrics properties are summarized in Table 1. Yarns are composed of 6 yarn ends for warp yarns direction and 4 yarn ends for weft yarns direction. The final yarn count is reported in the table below, with a reduction of 19.6% for hollow fibers warp yarns and 19% for hollow fibers weft yarns. The setting parameters for fibers production have conducted to an acceptable reduction in weight of the yarns (equal length). A major Italian company produced flat woven fabrics with a Jacquard loom, using hollow and full section fibers yarns. Woven fabric is the most used for seat cover application (Pamuk, 2008) and consists of two sets of yarns interlaced at right angles to each other. Its strength and durability can be varied and depend on the yarn type and the thread spacing (Horrocks and Arnand, 2016). For this research, woven fabric structure type is twill weave. Three samples with different number of weft yarns/cm have been considered to notice the influence of yarns density on the results and to better evaluate global fabrics characteristics.
Fabrics were subjected to further processes: dry cleaning with C2Cl4, thermo-fix process at 140°C and calender process to optimize dimensional stability. As some authors tell (Becerir et al., 2007), hollow fibers can compromise wear resistance of the final product. For this reason, double washing during the production process was done, to better eliminate impurities and weaving oils. The last production step is a lamination process. It is applied to almost every kind of fabric in the automotive sector and it impart a soft touch to the fabric and ease the sewing process of cover manufacturing. During this step, a flame lamination step, the polyurethane is the adhesive, melted with a gas flame. The fabric manufacturer laminated fabrics to one side of a polyurethane foam layer and a scrim fabric to the other side of the polyurethane layer (Fung and Hardcastle, 2001). In Table 1, values of fabrics total thickness and fabrics total weight are referred to laminated fabrics with polyurethane layer foam and the scrim fabric, instead fabric weight and thickness refers to the fabric itself, without lamination.
As visible in Table 1, hollow and full fibers fabrics weight is different and we can evaluate a 20% average reduction in weight for the fabric without lamination. This reduction reflects reduction of the yarn weight with the yarn count, as mentioned above with data reported in Table 1. Each hollow section fibers sample has been compared to its respective full section fiber sample. The evaluation has been done on five samples for each kind of fabric. In particular, the reduction in weight is 20.1% for 13 weft yarns/cm sample, 20.7 and 20.9% for 14 and 15 weft yarns/cm samples, respectively. Instead, total laminated weight can change depending on the variability of polyurethane and scrim fabric weight and thickness and on the variability of the sampling.
Tensile and tear resistance tests were performed to evaluate fabrics mechanical characteristics. Fabrics need to bear seat cover manufacturing processes and to perform highly when exposed to mechanical stress throughout the lifetime of the vehicle. Tensile strength test was performed on Acquati AG/7E/306 electronic dynamometer according to ISO 13934-1 (Iso 13934-1:2013, 2013). For each type of fabric, five samples for warp and five for weft direction were tested. This is necessary because fabric properties are affected by the loading direction. Tear strength test was carried out to measure the force to propagate a tear in fabric. This test is useful to evaluate the textile material stress suffered during the process of cover production. The test was performed according to ISO 9073 (ISO 9073:1999, 1999). Samples were prepared in the format as in Figure 2 and tore on one side (“cut” in Figure 2). The dashed lines point out where the clamps of the dynamometer grab the sample.
According to internal automotive validation test, perforation resistance test has been evaluated. This test reproduce the stress suffered from the fabric of seat cover when a foreign body accidentally perforates it, during the lifetime of the vehicle. The test was performed with the dynamometer and the particular device as in Figure 3, placed instead of the clamps, made up of a metallic sphere of 12.7 mm diameter. With the help of the dynamometer, the sphere moves at 80 mm/min and produce a perforation of the round sample.
Structural wear resistance was evaluated to define the resistance of the yarns composing the fabric. The test was performed on a Taber (Rotary Platform Double Head Tester) abrasimeter, according to ASTM D3884/09 (ASTM D3884/09:2013, 2013). The analyzed fabric was worn against two Calibrase 10 abrasive wheels, moving in opposite directions on its surface, as schematized in Figure 4. Three samples for each type of fabric were examined. According to internal automobile specification, 600 cycles of wheels rotation were set for woven fabrics. Flat woven fabrics require a longer period of testing because of their inherently more resistant structure, compared to other kinds of fabric structure, such as knitted ones.
Furthermore, worn surfaces were visually examined and graded by setting values from 3, best result with no yarns breakage, to 1, worse result, with at least a yarn breakage.
Aesthetic wear resistance of all type of fabrics was evaluated with a Cesconi Abrasive tester, comparable to Martindale Abrasimeter, according to ISO 12947/1-2-3-4 (ISO 12947/1-2-3-4:1998, 1998). This test reproduces the mechanical stress suffered by seat cover fabrics during their use for an average lifetime of the vehicle. The abrasion tester is generally used for testing textile materials. The apparatus is schematized in Figure 5. The abrading standard fabric is made of woolen fibers and fixed on a given plate (point A in Figure 5). The tested surface is placed on a rotating disk located under the fixed plate. The rotating plate moves with a revolution movement in order to ensure a complete wear of the fabric sample. 3000 and 6000 cycles were performed with a load of 3 kg, according to internal automobile validation test.
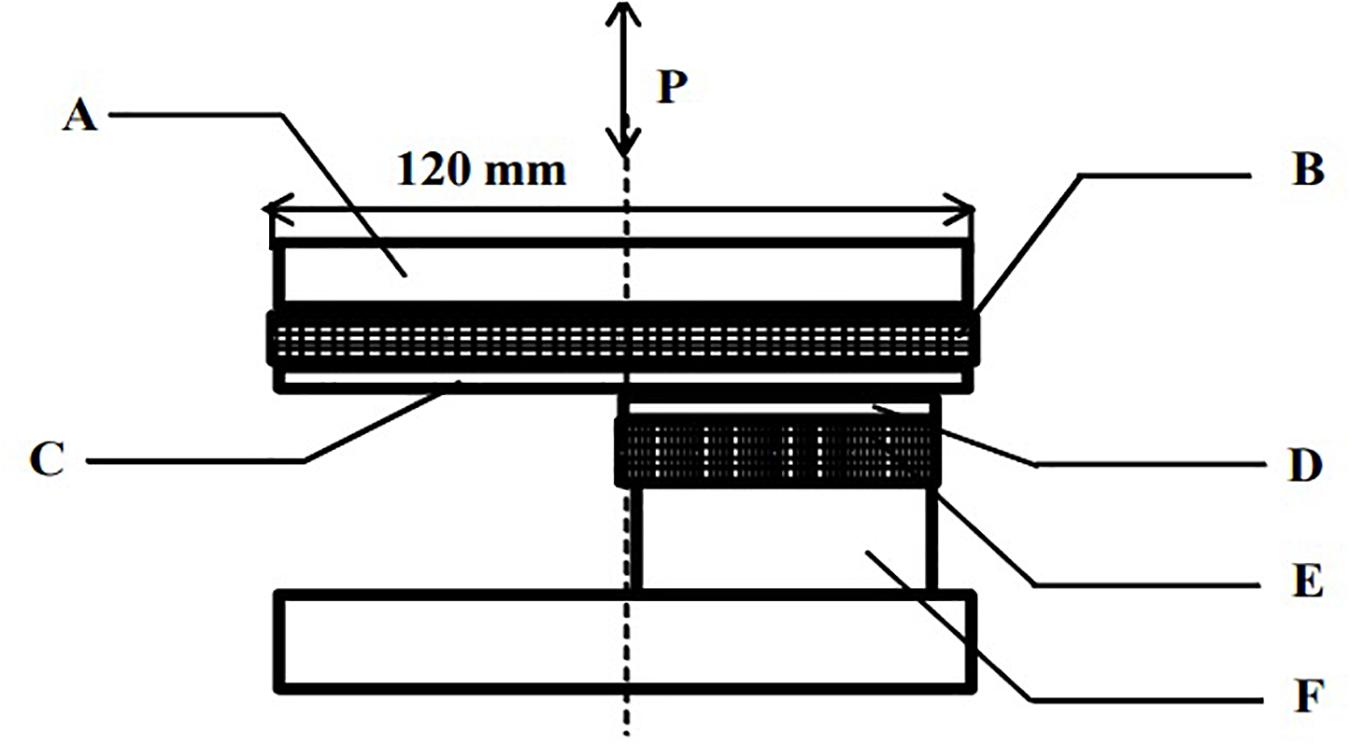
Figure 5. Scheme of wear resistance test apparatus. The substrate to test (D) is placed on the rotating plate (F), through a substrate holder (E). The abrasive fabric, instead, is placed on the fixed plate (A), using an appropriate substrate holder (B), on which a load is applied (P).
For aesthetic wear resistance test three samples for each kind of fabric were examined and evaluated according to gray scale. The scale quantifies changes in color compared to the reference. It includes a range of shade of gray, from 1, worse result, evident modification of the surface to 5, better result, almost no superficial changes on fabric, with a step of 0.5. Minolta CM-3610 spectrophotometer provided gray scale measurements, under a D65 illuminant using a 10° standard observer with specular component excluded (SCE) mode. Not worn surfaces were taken as standards and worn fabrics as samples. Surfaces pictures were recorded with LEICA M205C optical microscope. Before the tests, all specimens were conditioned for 72 h in a standard atmosphere at 20 ± 2°C with 65 ± 2% relative humidity, according to ISO 139 (ISO 139:2005, 2005).
Results
Hollow and full sections have been compared in Figure 6, which shows fibers transversal section.
On the left, the hollow section of the fibers is visible.
The average diameter of the fibers is 17 μm for hollow section and 19 μm for full section. The inner average diameter of hollow section is 8 μm.
Tensile Strength Test
Figure 7 shows strength resistance test for all kind of fabrics. Three samples (Table 1) have been tested: sample 1 (13 weft yarns/cm); sample 2 (14 weft yarns/cm) and sample 3 (15 weft yarns/cm).
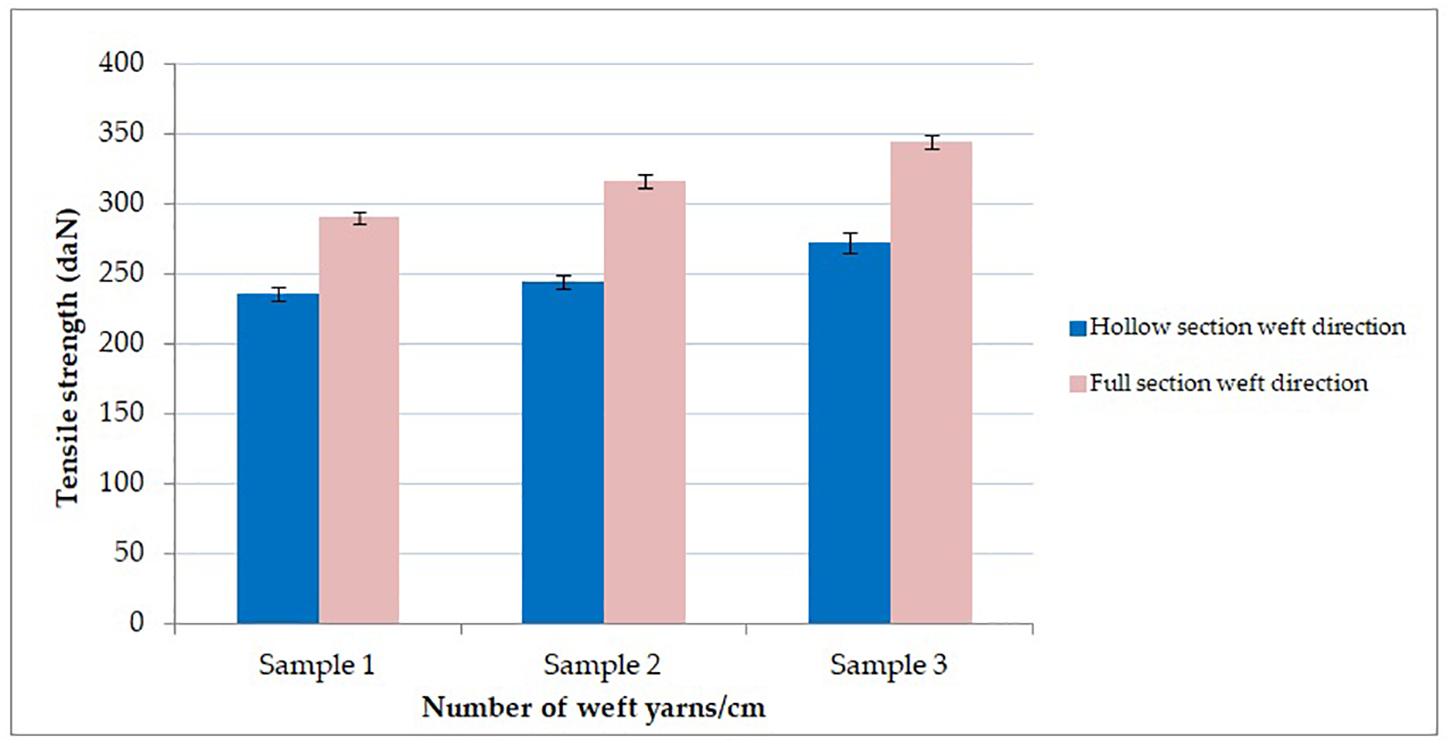
Figure 7. Tensile strength results. Hollow and full section and different number of weft yarns/cm have been evaluated.
Considering warp direction samples, they are all above automotive requirements (≥100 daN) and they don’t break under a force of 500 daN, the maximum load detectable for the dynamometer cell. High loads are required during fabric manufacturing and covers assembling steps. These results depend on the particular flat woven structure of the fabric and on the high number of warp yarns/cm. During the test, all warp yarns are stressed simultaneously and contribute to the result. There is no significant difference between hollow and full section fibers fabrics, and hollow section fibers do not seem less strong than full section fibers. Instead, considering weft direction samples, for both hollow and full sections, the load increase with the number of weft yarns/cm, as expected.
Tear Strength Resistance
In order to evaluate hollow section fibers fabrics performance tear strength test has been performed. Figure 8 shows the results with a comparison between hollow and full section fibers fabrics with different number of yarns/cm.
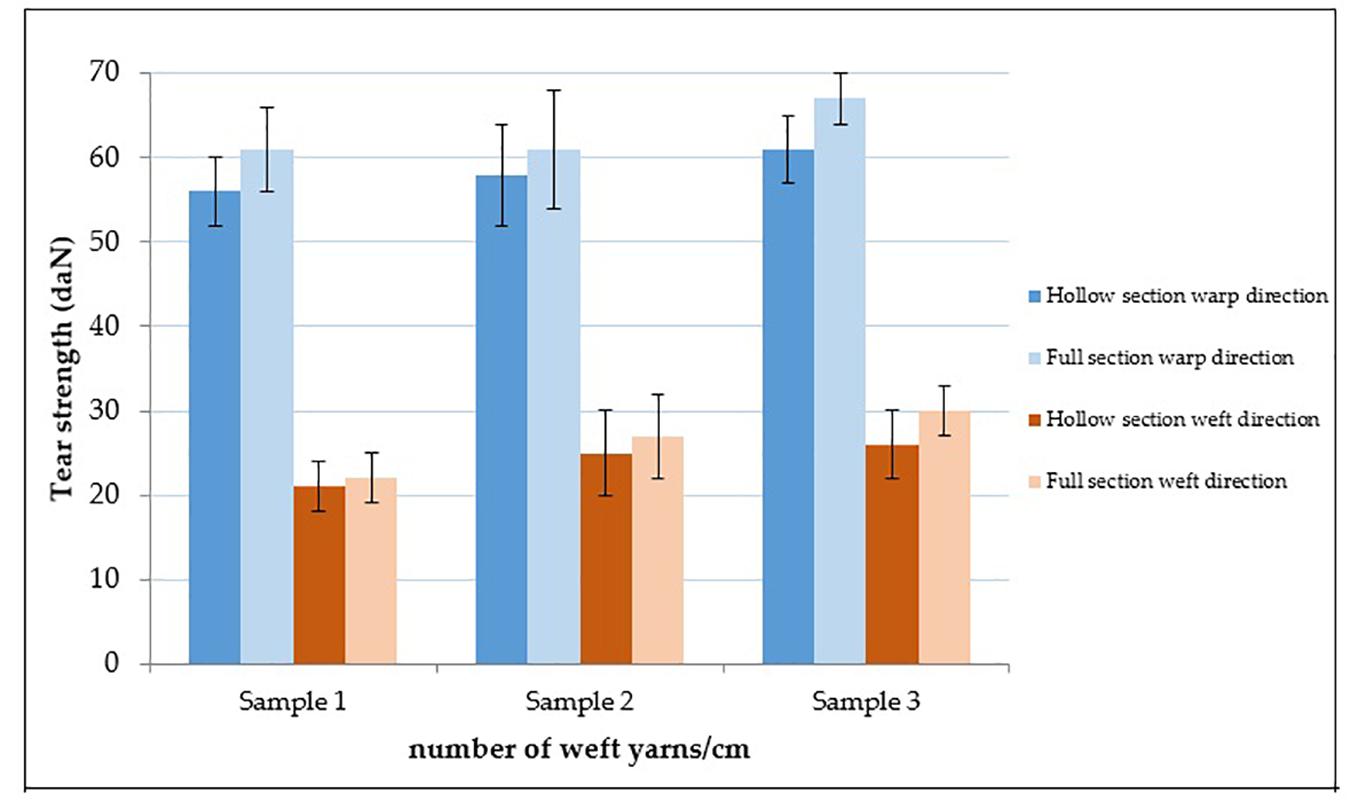
Figure 8. Tear strength results for warp and weft direction samples. Hollow and full section and different number of warp yarns/cm have been evaluated.
Tear strength resistance of hollow fibers fabrics is slightly lower than full fibers fabric, but almost comparable to them. This difference is kept for weft direction samples (Figure 8). Maximum load values are higher for warp direction samples, compared to weft direction samples. This is due to higher number of yarns/cm, 24, compared to 13, 14, and 15 for weft direction samples. Among three different yarns density sample there are not significant differences, considering standard deviation, so they are all considered comply with automotive standards.
Perforation Strength
Figure 9 shows perforation strength results for hollow and full section fabrics. Different number of warp yarns/cm have been evaluated. Current production fabrics are perforation resistant, with high average values included between 130 and 134 daN. Hollow section fibers fabrics show slightly lower values of perforation strength, due to the particular fiber section, but acceptable according to automotive standards, for which 25 daN minimum is required.
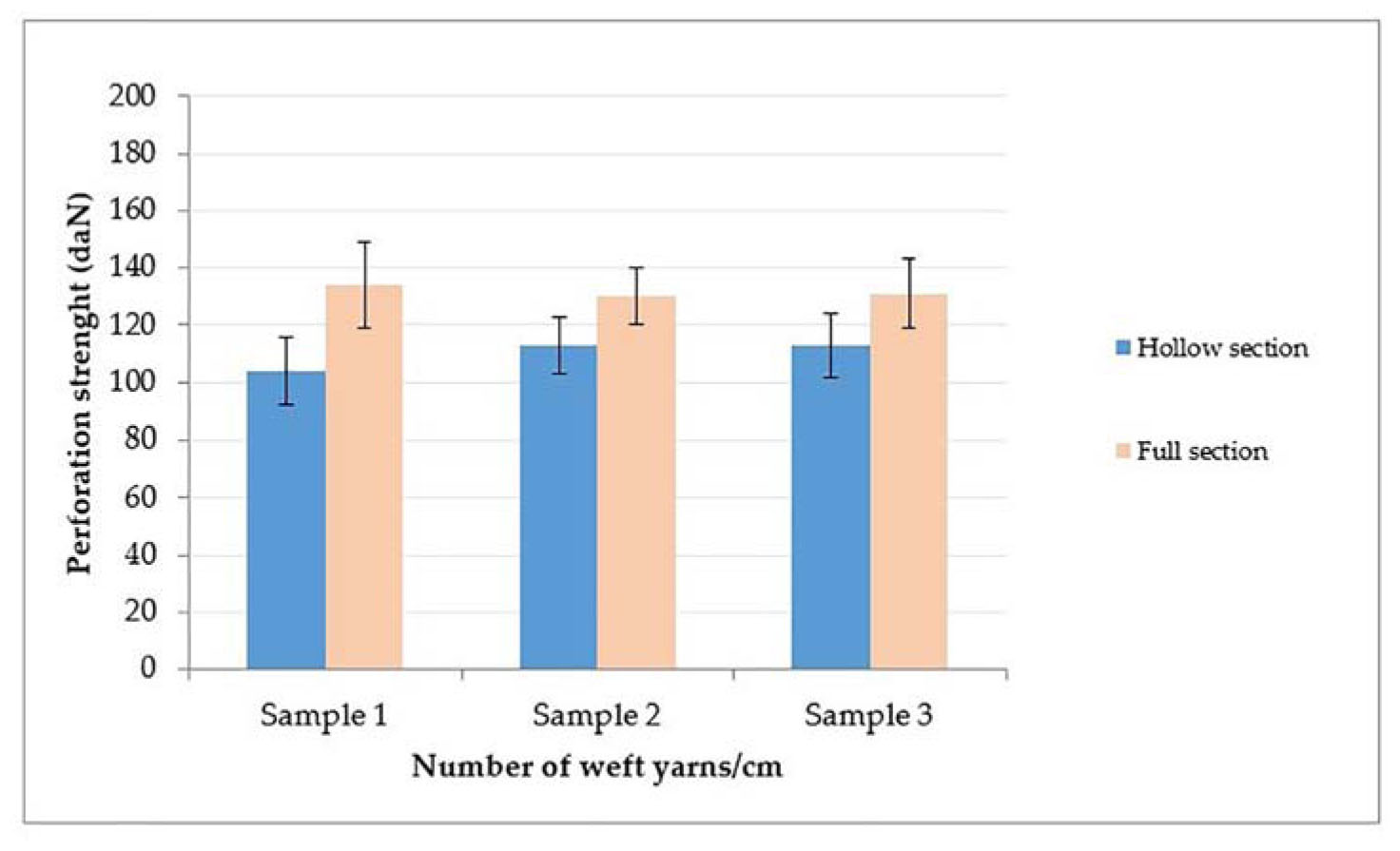
Figure 9. Perforation strength results. Hollow and full sections and different number of warp yarns/cm have been evaluated.
Abrasion Resistance
For all kinds of fabrics, structural wear resistance results are summarized in Table 2. Not worn fabrics were taken as standard fabrics, and they are evaluated grade 3. After Taber test, full section fibers fabric does not show any yarn breakage, nor structural changes. The worn surface presents a slight shadow, hence it’s evaluated grade 3. This result is positive according to automobile standard, for which there must be no yarns breakage.
Sample 1 surface, composed of hollow section fibers, shows some fibers/yarns breakage after structural wear resistance test, compared to sample 2 and 3. The abrasive wheels stress their surface several times and cause the damage of the most superficial fibers. Sample 1 has lower weft yarns density and this can have influence on the result. Furthermore, the hollow structure of the fiber and the less number of weft yarns/cm compared to sample 2 and 3 affect the result.
Afterward, fabrics surface was examined after aesthetic wear resistance test. Values of gray scale have been registered with the spectrophotometer and they are represented in Table 3.
For a more accurate analysis, pictures of the surfaces have been taken at different magnification with an optical microscope (Figures 10–12). Worn surfaces of full section fibers fabrics do not present broken yarns nor structural modifications. Hollow section fiber fabrics (sample 1, 2, and 3) show evident modification of the surface after 3000 cycles, fibers lifting and breakage and clear whitening of the surface. After 6000 cycles, the surface has lifted fibers and disappearing of fabric structure but it is not worse compared to 3000 cycles results. This is confirmed by gray scale values: their surfaces are evaluated 2 of gray scale after 3000 and 6000 cycles (Table 3), unacceptable according to automotive standards. Despite the slightly better gray scale evaluation (Table 3), sample 1 (hollow section) surface appearance is visually the worst compared to sample 2 and 3, because of lifting and damaging of the fibers. This is a consequence of a difference in yarns density and structural weakness, as observable also after Taber abrasion test (Table 2). Full fiber fabrics bear the abrasive wheels stress of surface and they are evaluated 4.5 of gray scale after 3000 cycles and 4 after 6000 cycles.
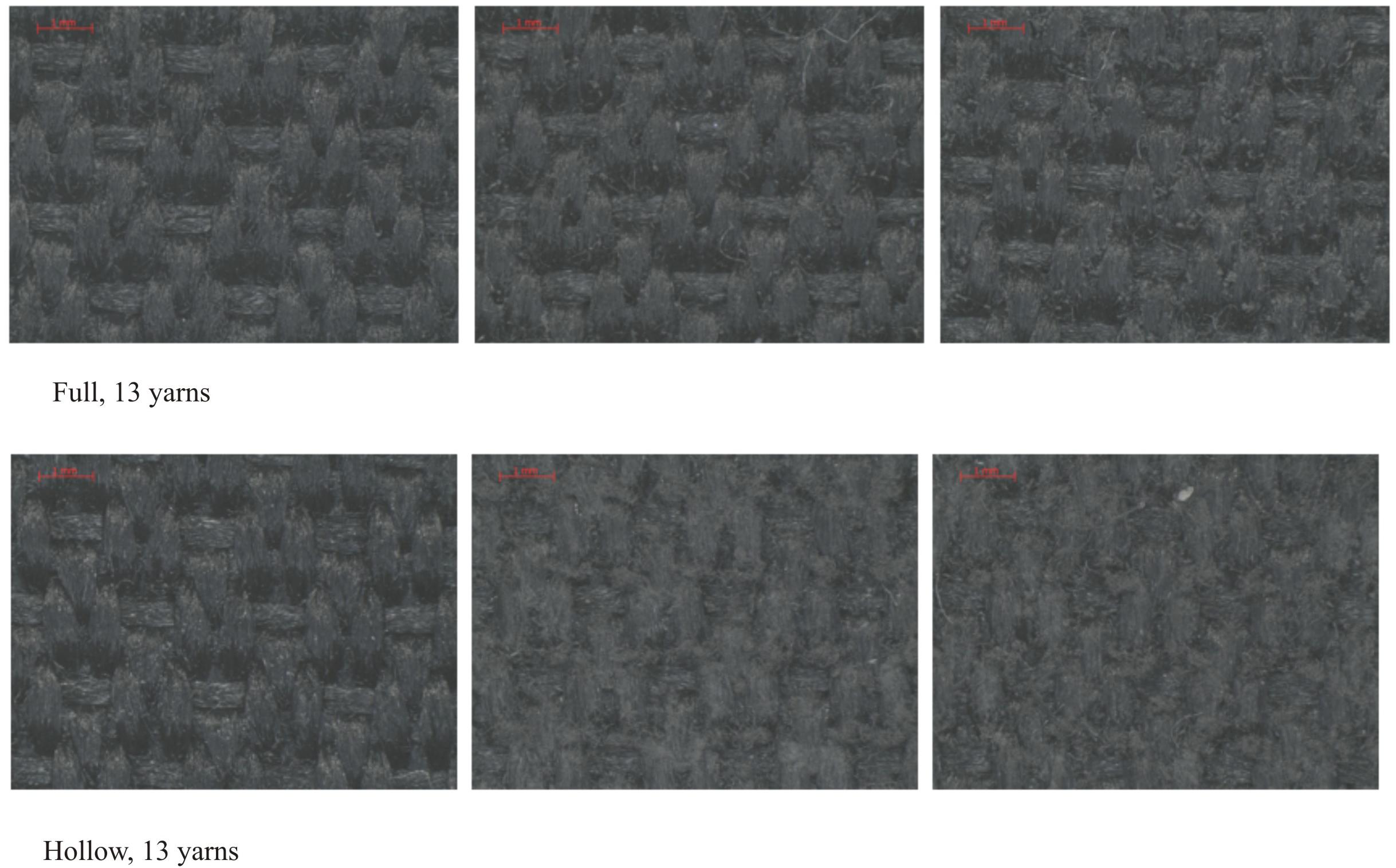
Figure 10. Pictures under the microscope of full and hollow section 13 weft yarns/cm PET fabric surfaces before wear resistance test and after 3000 and 6000 cycles of wearing (from left to right).
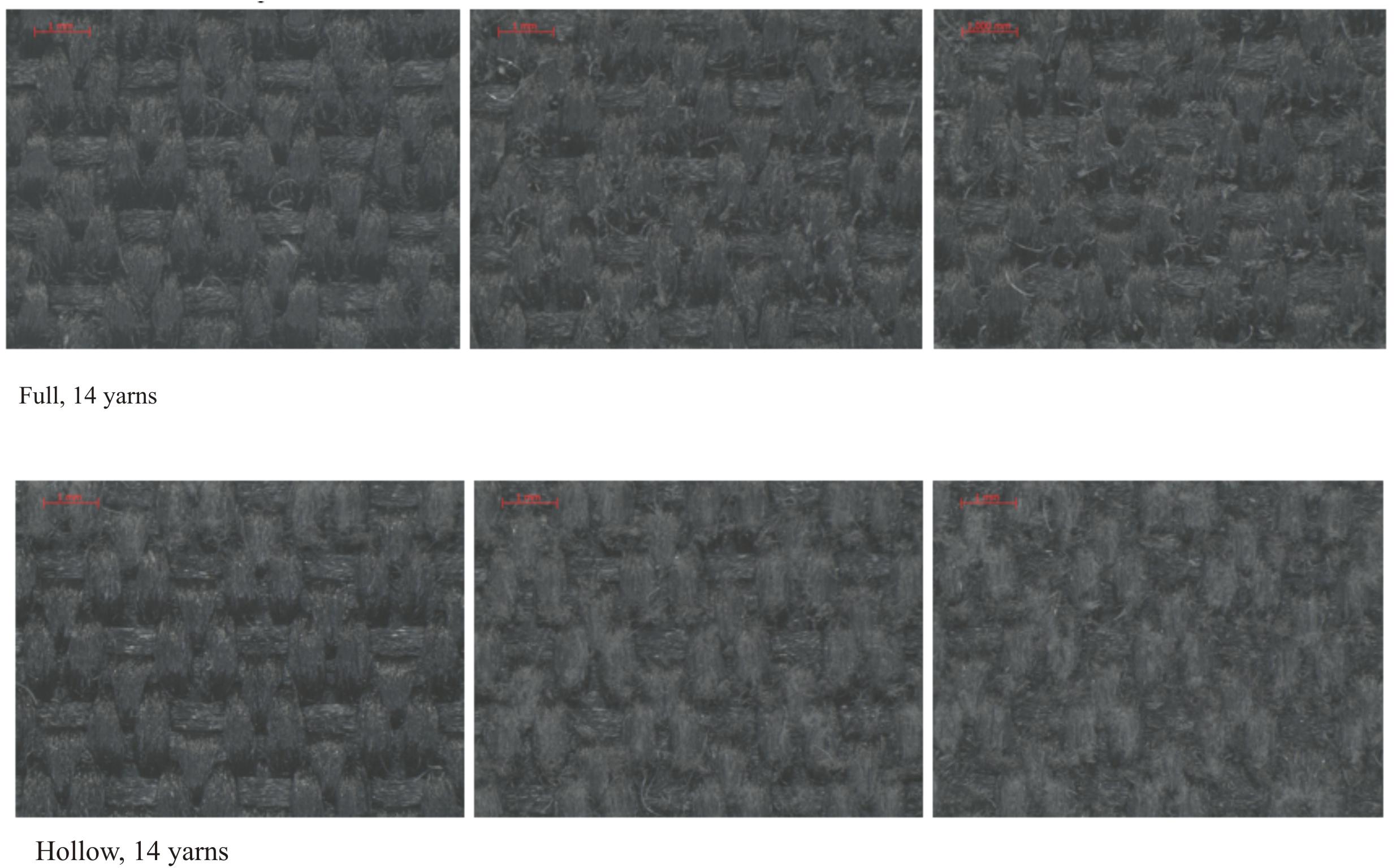
Figure 11. Pictures under the microscope of full and hollow section 14 weft yarns/cm PET fabric surfaces before wear resistance test and after 3000 and 6000 cycles of wearing (from left to right).
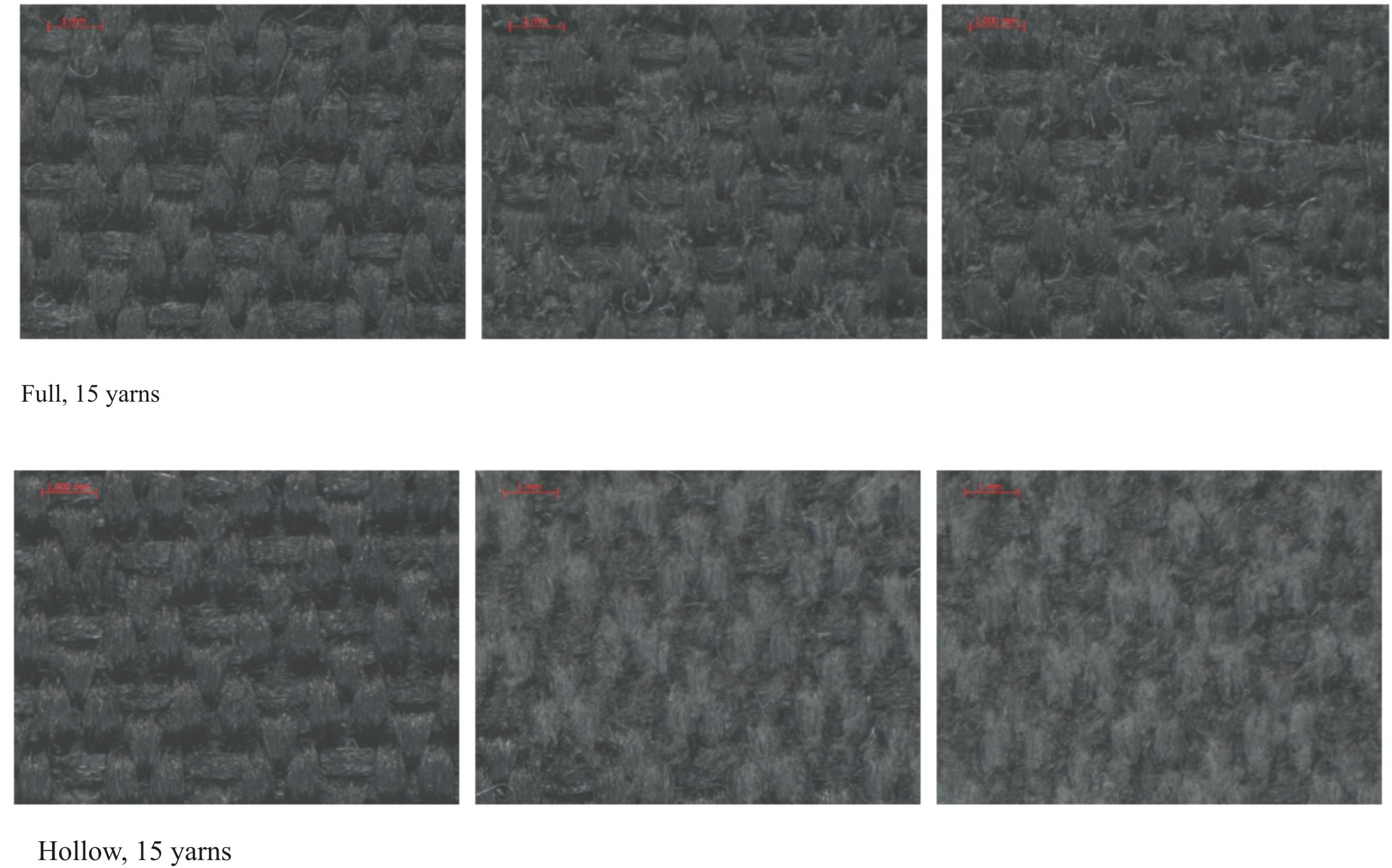
Figure 12. Pictures under the microscope of full and hollow section 15 weft yarns/cm PET fabric surfaces before wear resistance test and after 3000 and 6000 cycles of wearing (from left to right).
For both structural and aesthetical, wear resistance depends on a combination of fiber structure, yarn, and fabric construction characteristics.
Conclusion
In this paper, structural and mechanical characteristics of PET fabrics composed of hollow section fibers were evaluated. They were compared to current production full section fibers PET fabrics. Mechanical tests were performed to evaluate their matching with specific automotive requirements.
Despite good mechanical results, hollow section fibers fabrics can’t be applied as cover of very contactable areas, for example sittings areas and back seats. In fact, structural and aesthetic wear resistance test results showed fibers breakages and lifting and structure disappearing. For this reason, they are not in compliance with automotive regulations. Otherwise, hollow section fibers fabric is suitable as “covering textile” for less contactable areas, lateral zones, ceiling, door panels, etc. With these specific applications, negative effects of aesthetic abrasion may be avoided. Hollow fibers fabric reaches the elevated mechanical performance of current production PET textile materials, and it can replace them where aesthetic abrasion cannot compromise its use. A slight difference has been found among the three hollow section fiber samples tested, regarding abrasion resistance test result for 13 warp yarns/cm density fabric (sample 1). This result can direct fabric choice toward sample 2 and 3, to gain a durability for the lifetime of the vehicle.
Hollow section fiber fabrics can contribute to benefits as reducing vehicle weight of approximately 20% compared to current production textiles materials, being applied as covering of specific parts of car interior. In this way, these fabrics can be environmentally friendly.
Data Availability Statement
All datasets generated for this study are included in the article/supplementary material.
Author Contributions
VB and BP designed the experiments. GA performed the experiments. GA and VB analyzed the data. VL revised the manuscript. All the authors reviewed and approved the manuscript.
Conflict of Interest
The authors declare that AUNDE provided materials analyzed in this work. AUNDE did not provide funding and was not involved in the study design, collection, analysis, interpretation of data, the writing of this article or the decision to submit it for publication.
Acknowledgments
The authors wish to thank AUNDE for fabrics production.
References
Albini, G., Brunella, V., Lambertini, V. G., Placenza, B., and Martorana, B. (2019). Comparative study of mechanical characteristics of recycled PET fabrics for automotive application. J. Ind. Text. 48, 992–1008. doi: 10.1177/1528083717750887
Andreoli, C., and Freti, F. (2004). Man-Made Fibres – Reference Book of Textile Technologies, 1st Edn. Milano: Fondazione Acimit, 37–48.
ASTM D3884/09:2013 (2013). Standard Guide for Abrasion Resistance for Textile Fabrics - Taber Method. West Conshohocken, PA: ASTM.
Becerir, B., Karaca, E., and Omeroglu, S. (2007). Assessing colour values of polyester fabric produced from fibres having different cross-sectional shapes after abrasion. Color. Technol. 123, 252–259. doi: 10.1111/J.1478-4408.2007.00092.X
Cole, G. S., and Sherman, A. M. (1995). Light-weight materials for automotive applications. Mater. Charact. 1995, 3–9. doi: 10.1016/1044-5803(95)00063-1
Eichhorn, S., Hearle, J. W. S., Jaffe, M., and Kikutani, T. (2009). Handbook of Textile Fibres Structure, 1st Edn, Vol. 2. Cambridge, MA: Woodhead Publishing, 328–391.
Fredriksson, L., and Veitl, A. (2011). Automotive Development: All Eyes on CAE Weight Managemen. Avaliable at: http://blog.altair.co.kr/4251 Presentation of Altair (accessed December 23, 2011).
Fung, W., and Hardcastle, M. (2001). “Introduction survey,” in Textile in Automotive Engineering, 1st Edn, ed Woodhead Publishing (Cambridge, MA: Woodhead Publishing), 1–23.
Hearle, W., and Morton, W. (2008). “An introduction to fibres structure,” in Physical Properties of Textile Fibres, 1st Edn, ed Woodhead Publishing (Cambridge, MA: Woodhead Publishing), 1–81. doi: 10.1533/9781845694425.1
Horrocks, A. R., and Arnand, S. C. (2016). “Technical fabrics structures-woven fabrics,” In Handbook of Technical Textile, 2nd Edn, Eds A. R. Horrocks, S. Anand, and S. C. Anand Vol. 2. Duxford: Woodhead Publishing, 62–94. doi: 10.1533/9781855738966.62
ISO 12947/1-2-3-4:1998 (1998). Determination of Abrasion Resistance - Martindale Method. Geneva: ISO.
Jambor, A., and Beyer, M. (1997). New cars, new materials. Mater. Design. 1997, 203–209. doi: 10.1016/s0261-3069(97)00049-6
Khoddami, A., Carr, C. M., and Gong, R. H. (2009). Effect of hollow polyester fibres on mechanical properties of knitted wool/polyester fabrics. Fibre Polym. 10, 452–460. doi: 10.1007/s12221-009-0452-7
Ki-Young, K., Song, J. D., and Jung, N. I. (2013). Effects of binder fibres and bonding processes on PET hollow fibre nonwovens for automotive cushion materials. Fibre Polym. 2013, 639–646. doi: 10.1007/s12221-013-0639-9
Koch, H. J. (2005). Reducing CO2 Emissions from Cars. Dessau-Roßlau: German Advisory Council on the Environment.
Lukay Nonwoven Solutions (2019). Lukay Nonwoven Solutions. Available online at: http://www.lnws.eu/it/prodotti/pacchifiliere/ (accessed February 18, 2019).
Lyu, M. Y., and Choi, T. G. (2015). Research trends in polymer materials for use in lightweight vehicles Int. J. Precis. Eng. Man. 2015, 213–220. doi: 10.1007/s12541-015-0029-x
Mahmoud, A., El-Shenawy, G., and Ramadan, E. (2011). Using nonwoven hollow fibres to improve cars interior acoustic properties. Life Sci. J. 8, 344–351.
Matsudaira, M., Tan, Y., and Kondo, Y. (1993). The Effect of fibre cross-sectional shape on fabric mechanical properties and handle. J. Text. I. 84, 376–386. doi: 10.1080/00405009308658970
Official Journal of the European Union (2009). Regulation (EC) 443/2009 of the European Parliament and of the Council Setting Emission Performance Standards for new Passenger Cars, as Part of the Community’s Integrated Approach To Reduce CO2 Emissions From Light-Duty Vehicles. Brussels: Official Journal of the European Union.
Pamuk, G. (2008). Comparative study of the abrasion resistance of automobile seat covers. Fibres Text. East. Eur. 16, 57–61.
Keywords: hollow fibers, PET fibers, automotive fabric, technical textile, weight reduction, emission reduction
Citation: Brunella V, Albini G, Lambertini VG and Placenza B (2020) Hollow Section Fibers Characterization for Seats Covers Fabric Application. Front. Mater. 7:243. doi: 10.3389/fmats.2020.00243
Received: 18 February 2020; Accepted: 03 July 2020;
Published: 04 August 2020.
Edited by:
Emilia Morallon, University of Alicante, SpainReviewed by:
Antonio Greco, University of Salento, ItalyPhilippe Boisse, Institut National des Sciences Appliquées de Lyon (INSA Lyon), France
Kadir Bilisik, Erciyes University, Turkey
Copyright © 2020 Brunella, Albini, Lambertini and Placenza. This is an open-access article distributed under the terms of the Creative Commons Attribution License (CC BY). The use, distribution or reproduction in other forums is permitted, provided the original author(s) and the copyright owner(s) are credited and that the original publication in this journal is cited, in accordance with accepted academic practice. No use, distribution or reproduction is permitted which does not comply with these terms.
*Correspondence: Valentina Brunella, valentina.brunella@unito.it