Definition and Exploration of the Integrated CO2 Mineralization Technological Cycle
- 1Laboratoire de Génie Chimique, Université de Toulouse, CNRS, INPT, UPS, Toulouse, France
- 2Laboratoire Matériaux et Durabilité des Constructions, Université de Toulouse, INSA, UPS, Toulouse, France
This paper is part of a multi-disciplinary research program on development and application of an integrated CO2 mineralization (ICM) framework for development of carbon mineralization as a CO2 mitigation solution. ICM is viewed as a three concentric layer system: technological, industrial integration, and decision-making. The search for viable ICM solutions in a given societal and economic context, which could be posed as an inverse design problem, begins with the identification and characterization of every system component. As an early writing on the development and applicability of the proposed ICM framework, this contribution focuses on ICM's inner technological layer. Several technological pathways, each one defined as a set of processing and transformation steps that connect a feedstock to a specific marketable product, can coexist within this layer. The paper addresses the characterization of one such technological pathway, whose cycle is divided into three successive blocks: feedstock, carbonation and valorization. The proposed concepts are illustrated through the valorization of ferronickel slag from New Caledonia as supplementary cementitious material or cement constituent, a case study that targets the production of “greener” construction materials. The data presented in the paper confirm the feasibility of characterizing the chosen ICM technological pathway, giving credit to the proposition that ICM can be approached as an inverse design problem. While exemplifying the significance of the characterization work necessary for one particular ICM technological pathway, the paper argues that development of ICM requires working on a scale considerably larger than that of standard mineral carbonation process research. Indeed, where grams of carbonated products are sufficient to investigate mineral carbonation processes, kilograms are mandatory to test and validate the use performance of final marketable products. Without precluding the merits of seeking innovative solutions, the authors argue that unit operations and transformation processes whose validity is proven at an industrial scale should be favored for timely development of viable ICM solutions.
Introduction
Around the turn of the century, the international CCS community focused on developing and testing CO2 geological storage solutions on a large scale, by diverting proven oil industry technologies and expertise from their usual uses. The geological storage community explored and identified different types of large reservoirs, and enhance oil recovery (Damen et al., 2005) provided technological developments with early economic incentives to move forward.
The mineral carbonation research community concomitantly followed Seifritz's (1990) geo-inspired large-scale process proposition to bring pressurized CO2 into contact with an aqueous suspension of silicate particles to trap CO2 in the form of solid carbonates. Research efforts focused on developing processes to carbonate natural silicates, whose worldwide abundance meant a massive potential for CO2 storage (Picot et al., 2011). Mineral carbonation did not however benefit from the same starting point as geological storage. Indeed, there was no readily available technology, and perhaps more importantly, no early economic opportunity nor governmental incentive that would place a sufficient price on carbon emissions to support large-scale mineral carbonation projects. Mineral carbonation research focused on finding ways to reduce the natural silicates' weathering process geological time scale to an industrial time scale. The research community rapidly mapped out and investigated a number of process routes, considering dry/aqueous and direct (single-stage)/indirect (multi-stage) processes with natural and waste materials, with and without pretreatments (Sanna et al., 2014). The highest carbonation yield and kinetics were obtained with aqueous mineral carbonation processes, which took different technological forms, such as pH-swing (Azdarpour et al., 2014), PCO2-swing (Rim et al., 2020), and attrition-leaching (Julcour et al., 2014) to name a few.
With the emergence of CO2 utilization research and the modified acronym CCUS, came the recognizance that mineral carbonation products could be valorized, which shed a completely new light on mineral carbonation. This provided mineral carbonation with economic incentives that had been missing until then. From then on, mineral carbonation was accepted as a potentially worthy CO2 utilization solution. According to the IEA (International Energy Agency, 2016), these are solutions which, (1) have the potential to achieve significant emissions reduction, (2) can generate revenue to offset their implementation costs, and (3) are scalable to scales commensurate with large CO2 point sources. Mineral carbonation is becoming more and more commonly referred to as carbon or CO2 mineralization (Power et al., 2013), which reflects its established legitimacy as a CO2 utilization solution (Mission Innovation, 2018; National Petroleum Council, 2019).
However, turning the mineral carbonation processes, as envisioned by Seifritz (1990) into worthy CO2 mineralization solutions is no simple undertaking. Indeed, successful development of CO2 mineralization depends on its becoming an integral part of a viable economic framework, hence the term “integrated CO2 mineralization” used by the authors, or ICM for short. It must use resources available on a given region or territory to produce commercializable materials that meet identified market needs. In order to develop realistic ICM solutions for a given territory, it is necessary to carry out a decision-making analysis using economic, societal and environmental criteria acceptable for the territory in question.
Elements of Integrated CO2 Mineralization (ICM) Framework
The development of ICM is therefore a complex integrated process, which takes into account many interconnected variables and constraints specific to the territory where its deployment is intended. Development of realistic ICM solutions on a territory requires an iterative construction between the systemic and technological scales of the problem, which can be described by three concentric interconnected ICM layers shown in Figure 1:
- The technological layer is the inner ICM layer, which is characterized by process solutions that transform a natural or waste feedstock into a useable product. This layer may comprise several possible pathways, each pathway combining particular carbonation and valorization processes to produce one type of valuable product. This is the layer to which this paper is mostly dedicated, which the authors refer to as ICM's technological cycle, as it requires a number of successive processing and material transformation steps.
- The industrial integration layer is the intermediate ICM layer, whose purpose is the scaling and transposition of the technological cycle pathways to industry. This layer requires retrofitting process solutions to one or more existing industrial sites and/or developing dedicated plants.
- The supervisory or decision-making layer is the outer ICM layer, which uses economic, societal and environmental criteria to assess the actual viability of ICM solutions in a given context. This analysis uses a wide array of performance indicators, including, but not limited to, standard Life Cycle Analysis (LCA) indicators such as Global Warming Potential over 100 years (Joint Research Centre, 2011), economic indicators related to the competitiveness of ICM products against their standard counterparts, and market indicators that quantify the adequacy between production and consumption flows. The reader is directed to Ventura and Antheaume (2019), who have proposed a consistent LCA methodology as a solution for the ICM supervisory layer. This methodology is an extension of substitution scenarios and consequential LCA for the constrained markets for which ICM solutions are intended.
Development and implementation of ICM is akin to an inverse design problem (Kulkami et al., 2014), whose solving prerequisite is the mapping and characterization of all the links within and between the three ICM layers from Figure 1. The search for realistic solutions to the ICM inverse design problem is a general optimization problem (Eden et al., 2004). In a given regional context, the problem formulation requires that all the individual elements of the ICM problem defined by Figure 2 be expressed as models and formal constraints, with associated uncertainties. Full development of viable ICM solutions is quite clearly a collaborative multi-disciplinary multi-sectorial endeavor, which represents a major change in paradigm compared to early mineral carbonation research.
Besides introducing concepts that underlie the authors' take on ICM, this paper makes no other claim than establishing and discussing the feasibility of characterizing the links that pertain to ICM's inner technological layer, where ICM's marketable products are construction materials, for which the demand is on a scale commensurable with the consumption of significant quantities of CO2. From this point forward, the paper focusses solely on the technological cycle of ICM's technological layer. This cycle includes a succession of transformation stages and products, the products of one stage of transformation becoming the inputs to the next stage. It makes sense to divide this production cycle into 3 blocks: feedstock, carbonation and valorization (Bourgeois et al., 2018).
- The feedstock block includes two components, the carbonatable material (industrial and mining waste, natural ore, brines) and the source of CO2 (industrial flue gas) intended for ICM's carbonation steps. Transformations may be necessary in order to prepare feedstock components before feeding them to the carbonation block. The material feedstock may require a grinding step to increase its initial specific surface area, or some degree of thermomechanical dehydroxylation to improve its intrinsic reactivity (Dlugogorski and Balucan, 2014). The CO2 source may also need to be purified and compressed in order to increase the CO2 partial pressure, one of the known carbonation controlling parameters. The feedstock conditioning step could also be allocated to the carbonation block; this choice is subjective, however the authors deemed it more sensible to position it in the feedstock block, since the material and CO2 feedstocks may not be physically located on the carbonation process site.
- The carbonation block is where carbonation reactions take place. It starts with the carbonation process, which can yield different products depending on the technology used and operating conditions thereof. Before moving on to the valorization block, carbonated products may require some post-carbonation steps. With aqueous carbonation for example, dewatering may be required for recycling process water.
- The valorization block is ICM's last and possibly most critical block from the standpoint of the viability of ICM. It is dedicated to the valorization of carbonation products. Before transforming carbonated products into valorizable products, this block may require some transformations. With building materials as marketable products, this could be a heating step to yield a binder, or an additional grinding step to produce a mineral addition. Valorizable products would then undergo a final transformation stage, to turn them into marketable products.
Although the paper has a clear focus on production of alternative commercial building materials, it is worth noting that ICM can be used to other ends, as with direct mineralization of naturally occurring calcium (Bukowski and Berger, 1979) or magnesium silicates (Winnefeld et al., 2019) using captured CO2 from industrials flue gases. With building materials, several aspects must be considered:
- The type of the final manufactured products (e.g., reinforced concrete, precast concrete, slabs, concrete blocks, tetrapods);
- The type of building structure (e.g., foundations, walls, bridges, roads);
- The class of environment of the final products, related to its use (e.g., corrosiveness and durability).
Consequently, several questions are invariably raised when manufacturing final products that incorporate ICM materials in relation to their performance in service: do final products have equal or improved mechanical performance to their standard counterparts? Is there a substantial modification in durability of the final products? These are some of the questions that will need to be considered when planning the characterization of the properties of valorizable products.
The interface between the carbonation and valorization blocks is perhaps the cornerstone of the ICM technological cycle. It is a challenging area of research at the crossroads between process and civil engineering fields. Indeed, it involves understanding the links between the properties of the products of these two blocks, and matching the transformation steps they contain to yield final products with the desired use properties. Developing realistic ICM solutions is no longer a question of designing energy efficient carbonation technologies; it is a matter of developing and optimizing the complete ICM technological cycle of Figure 2 as one global process, from the feedstock materials to the final commercial products. Significant research efforts address the various stages of this cycle, dealing with feedstocks of carbonatable materials (Bodénan et al., 2014), technological development of carbonation processes (National Petroleum Council, 2019), or utilization of carbonation products (Woodall et al., 2019).
In addition to offering a CO2 utilization solution, ICM is a possible response to the environmental problem raised by construction materials, and concrete in particular. Indeed, concrete is the most used building material worldwide and is responsible for about 5% of global CO2 emissions (Schneider et al., 2011). While standard concrete is made of Portland cement, aggregates (sand and gravel) and water, the clinkering process generates about 800 kg of CO2 per ton of cement produced, which represents 98% of concrete's CO2 emissions (see Figure 3).
ICM is a possible match for two of the portfolio of innovative solutions that concrete and cement manufacturers have identified to reduce these emissions (Schneider et al., 2011; Gartner, 2017). Besides switching to alternative fuels and developing dedicated CO2 capture technologies, the cement and concrete manufacturing industry has identified two types of materials related levers to reduce its carbon footprint (Spinelli et al., 2017):
- Materials used in concrete (a) to replace a fraction of the Portland cement, often referred to as Supplementary Cementitious Materials (SCMs), or (b) to replace a part of the clinker in Portland cement manufacture, to produce blended cements. These materials have been largely studied and commercial concretes/cements with reduced Portland cement/clinker content are already used. Depending on their chemistry and particle size, these mineral powders can have different behaviors in a cementitious environment: hydraulic (ground granulated blast furnace slag (GGBS), type C fly ashes), pozzolanic (type F fly ashes, silica fumes, natural pozzolans, metakaolins), or inert (calcite, quartz) (Kurdowski, 2014). Mineral powders can replace clinker in cement to various degrees, from 30% with pozzolans to 95% with GGBS, with a prorated reduction in cement carbon footprint. More is said about these materials later in this paper.
- Alternative binders whose production requires less energy and emits less CO2 than conventional cements. Alternative hydraulic binders include calcium sulfoaluminate, magnesium-based and alkali-activated cements (Schneider, 2019). In recent years, alternative non-hydraulic binders have received a great deal of attention, in particular carbonated calcium silicate cements, and have already led to commercial products (Atakan et al., 2014; Ashraf and Olek, 2016). They are typically produced using powdered belite or wollastonite as feedstock material. When exposed to an atmosphere with 100% humidity and 100% CO2, these powders harden due to the in-situ formation of calcite and an amorphous silica gel (Bukowski and Berger, 1979). The implementation of these new binders requires a source of CO2, which is trapped directly in the hardened construction material. Alternative binders that transform and trap CO2 during their making are attractive as complement to other cement industry's carbon footprint reduction levers, such as using alternative fuels, decreasing the cement to clinker ratio, using other alternative binders or improving the energy efficiency of current cement plants (Farnam et al., 2016). The use of alternative binders is included in reference scenario 2 according to the EU-agenda, which states the different technological roadmaps to reduce CO2 emissions in the construction sector by 2050 (Favier et al., 2018).
To explore whether ICM can actually be used for either of these pathways, the ICM template provided by Figure 2 must be applied to a real world case. The ICM application case under investigation by the authors is the production of commercial building materials from ferronickel slags produced by New Caledonia's nickel industry (Bourgeois et al., 2018). With 10% of the world's nickel reserves, New Caledonia ranks as one of the largest nickel producer in the world. Production, which is of the order of 200,000 metric tons per annum has increased in the past half-decade and is expected to continue in the near future. Current CO2 emission levels per capita in New Caledonia currently stand at 25 metric tons per annum, which is high by any standard. Half of these emissions are attributed to two large fossil-fuel powered Ni pyrometallurgical plants, which also produce 3 million tons of Nickel slag every year. It is noteworthy that the power stations, which are located on the pyrometallurgical sites, produce electricity for both the industrial sites and the New-Caledonian population. This situation is one example where both material and CO2 feedstocks are located on the same industrial site. The combined power of both power stations is in excess of 400 MW, and it is estimated that half their current CO2 emissions could be captured by mineralized slag on a stoichiometric basis (Bourgeois et al., 2018). Considering the scale of the New Caledonian mining industry and its significance to the local economy, with 20% of the territory's GDP, the favorable properties of Ni-slag as a mineralization feedstock, the insularity of the territory and its dependency on construction materials' import, and the setting of this southwest Pacific island and biodiversity (one part of New-Caledonia's lagoon is listed as a world heritage site), this project combines key ingredients of an interesting and significant integrated CO2 mineralization project (see Figure 4). The New Caledonian construction sector is not expected however to have the capacity to absorb all the products that can be produced by ICM of nickel slag, hence the ongoing research dealing with the ICM's outer supervisory layer is considering local and export markets as part of the evaluation of worthy ICM solutions.
The search for viable ICM pathways in this context—the solutions of the ICM inverse design problem—requires thorough characterization of all possible transformation steps that link the Ni-slag feedstock to sensible commercial products in the New-Caledonian context. Work to date has revealed the technical likelihood of several ICM technological pathways. For the sake of clarity, the technical likelihood of an ICM technological pathway does not mean that it is viable. As discussed earlier, technologically feasible ICM pathways must be linked to the industrial integration and supervisory layers, and it is only by seeking solutions to the inverse ICM problem that combines all three ICM layers that a given ICM technological solution may prove viable.
With the intent to explore the particulars of the characterization of ICM technological pathways, the paper focuses on a specific one: the production of supplementary cementitious materials (SCMs) from carbonated ferronickel slags. Figure 5 shows the transposition of the ICM generic template to this specific ICM technological pathway.
One constraint of the problem, which applies to carbonation block, is the use of the one-step aqueous attrition-leaching carbonation process developed by the authors (Julcour et al., 2014), which takes place inside a stirred media mill. For this ICM technological pathway, the interface between the carbonation and recovery blocks includes a dewatering step, for recycling water back to the aqueous carbonation process, followed by a drying step for reaching the right moisture content for materials handling and SCM making.
The next section considers the different products and transformation steps for the selected case study, considering each of the three blocks from Figure 5 in turn, with the aim of bringing out ICM technological cycle's most salient features, mainly from a characterization viewpoint.
Methodical Exploration of Integrated CO2 Mineralization (ICM)
The Feedstock Block
Ferronickel slag from New Caledonia is a magnesium-rich co-product of pyrometallurgical nickel extraction from lateritic nickel ores. They contain three main oxides: MgO, SiO2, and Fe2O3. Table 1 shows two chemical analyses measured 4 years apart, in 2015 and 2019. The slag compositional invariance with time is deemed an asset for the development of ICM solutions in New Caledonia, since processing plants operate at their highest efficiency with a steady feed. Moreover, this implies that old slag feedstocks can be reclaimed and mixed with new ones without disrupting the process.
The ferronickel slag feedstock from Table 1 is water quenched as it exits the pyrometallurgical furnace. The high cooling rate freezes the mixture at high temperature, whose composition is predicted by the forsterite/silica phase diagram (Bowen and Anderson, 1914) as made of crystalline forsterite and a vitreous phase of type MgSi2O5 (Umemoto, 2017). Co-characterization of crystalline and amorphous phases is one recurring challenge of ICM with industrial feedstocks. This challenge is addressed by coupling several analytical techniques. Crystalline phases were characterized by XRD with a Bruker D8 ADVANCE. Their proportions, as well as that of amorphous phase(s), were quantified by Rietveld analysis (performed with Topas software) using an external standard (zincite). A quantitative chemical analysis after total digestion of the material using sodium tetraborate as the melting agent was also carried out by ICP-AES (using a Mettler Toledo ICP-AES). This combined information permitted carrying out a full material balance (Full details will be published in a companion paper dedicated to characterization of feedstock and carbonated materials), which concluded the phase characterization of the ferronickel slag used in this case study. As shown in Figure 6, it is a mixture of ferrous forsterite (Fe0.22Mg1.78SiO4) and an amorphous magnesium silicate phase of formula MgSi2O5 (Mg/Si ratio = 0.5) as expected, with minor amounts of clinoenstatite (MgSiO3) and chromite (FeCr2O4).
Minor trace elements are a point of concern with ICM, hence their mineralogical form must be well-characterized also. Indeed, industrial wastes often contain a cocktail of elements, often metallic, which can be a health issue and need to be considered for the marketability of final products. The presence of undesirable elements may require additional transformation steps for their removal in the ICM cycle. In the case study, it was established that ferronickel slags contain chromium (measured by ICP-AES) in the form of chromite, where chromium displays a Cr(III) oxidation state. It is important to acknowledge the presence of this impurity, its content and oxidation state as the proportion of Cr(VI) is strictly limited in cements used in the construction sector. The EN-197-1 standard limit for Cr(VI) is 2 mg/kg in hydrated cement.
The quenching applied to the selected slag feedstock is a granulating process that produces millimetric slag particles. Currently, a dry grinding processing step is applied in the feedstock block to bring slag feedstock particles below 200 μm. The final particle size distribution (PSD), measured by laser diffraction after ultrasonication without dispersant using a Malvern MS3000, is shown in Figure 7. The PSD of feedstock particles is an important operating parameter in ICM, and will be the subject of further study.
The last element of the feedstock block is the CO2 source. This is an important point to consider since the performance of the aqueous mineral carbonation process is intrinsically sensitive to the partial pressure of CO2 (Cassayre et al., 2016). This is easily accounted for in carbonation process testing by varying CO2 partial pressure. It has obvious and direct implications on the need to pressurize the CO2 feedstock, and may lead to considering adding a CO2 capture step in the CO2 feedstock block of the ICM technological cycle. These aspects of the feedstock block are simple to integrate into the ICM inverse design analysis, given the flue gas composition and mass flowrate for the site considered. Indeed, the performance of flue gas' CO2 capture, treatment, and compression steps has been studied extensively and models exist for every such steps (Faruque et al., 2012a,b). Little is known however about the effect of minor elements present in the flue gas on mineral carbonation reactions. This issue is worthy of complementary research.
The Carbonation Block
The carbonation block of the ICM cycle starts with the carbonation process. Ideally, the reverse design approach to finding viable ICM pathways would require the availability of predictive models for all possible carbonation technologies. This is not yet possible however, as many such technologies are under development. This work uses a mineral carbonation technology developed by the authors, which is a single-step aqueous mineral carbonation process that operates inside a stirred media mill under temperature and pressure (Bonfils et al., 2012). The concept and implementation were born from several observations, a key one being the need for a continuous elimination of the passivation layers that form on the surface of feedstock particles during leaching. By combining the variability of potential feedstocks and the observed sensitivity of the nature of the passivating layers to variations in operating conditions (Julcour et al., 2014), the authors preferred their continuous elimination by physical means to their chemical control (Krevor and Lackner, 2011). This led to the development of what the authors refer to as the attrition-leaching mineral carbonation process, which merges attrition and leaching processes. Recently, the generic nature of the concept proposed by the authors for continuous elimination of passivating layers by attrition has been confirmed in the context of a study on the mineral carbonation process by PCO2-swing (Rim et al., 2020). By further considering the magnitude of the flow rates necessary for ICM to have meaning in terms of CO2 elimination, the authors decided to use to a technology proven at the scale of mining operations, which led them to the development of the mineral carbonation process inside a stirred media mill (Comminution Handbook, 2015). In practice (Jankovic et al., 2003), such mills can handle solids throughput in the 10 to 100 or more tons per hour, at solids concentration as high as 40% by mass. This technology also has the advantage of being scalable based on well-established energy criteria, allowing industrial reactors several cubic meters in volume to be sized from liter-scale laboratory reactors (Gao et al., 2001). This remarkable scaling property, important in the search for ICM solutions, is also an economic and practical asset for the development of realistic carbonation technology on a large scale from small pilot scale studies.
The attrition-leaching mineral carbonation process is a robust process whose performance was found to be largely insensitive to variations in operating conditions in the case of nickel slag. This gives strength to this process for ICM, and possibly for other feedstocks also. It is recalled that (Julcour et al., 2014) obtained similar results with natural silicate minerals. Figure 8 shows the carbonation rates obtained for minus 200 μm slag particles in a 300 mL stirred mill reactor, in 24 h, with the same grinding conditions (1 mm yttria-stabilized zirconia grinding beads, fixed stirring speed) in the operating temperature range (120–180°C) and CO2 partial pressure (2–20 bar). By deliberate choice, Figure 8 does not distinguish the conditions of each observation to highlight the stable performance of this mineral carbonation process for nickel slag. As shown in Figure 8, some conditions were repeated several times, while others were tested only once. In terms of carbonation extent, the attrition-leaching process exhibits a seemingly binary performance with nickel slag:
• Inside a wide range of temperature and CO2 partial pressure conditions (PCO2), the process yields a carbonation rate greater than 60%, irrespective of the test conditions. This relative invariance gives robustness to this mineral carbonation technology. In a first instance, its justifies developing an empirical mineral carbonation model based on aggregated observations for predicting the extent of carbonation and phase speciation as a function of time, with uncertainties, as a function of operating conditions, which can be used in the ICM inverse design problem. The extent of carbonation of the final product is measured by CHN and TGA for cross-validation. The final carbonation yield is then used to back-calculate carbonation yield at intermediate reaction times from pressure and temperature measurements in the CO2 reservoir that feeds the carbonation reactor (Julcour et al., 2014). After initial pathways are identified, it will be necessary to develop a mineral carbonation model that depends on the operating conditions. Indeed, a finer analysis of the results shows some influence of these parameters on the performance of the carbonation process. Furthermore, all of the data presented here were obtained for one slag PSD and fixed operating conditions of the stirred media mill, which can be modified to improve the extent and kinetics of carbonation.
• The attrition-leaching process yields a low carbonation extent (<30%) when the temperature and PCO2 conditions favor the formation of mineral phases that consume Mg other than carbonates, such as talc. At a given temperature, sharp changes in carbonation yield can be expected across short variations in CO2 partial pressure for instance from thermodynamic equilibrium considerations alone, as documented by Cassayre et al. (2016). This predictable behavior is related to changes in saturation indices of Mg-carbonate and Mg-silicate phases with PCO2, whose value may favor the formation of one phase at the expense of the other.
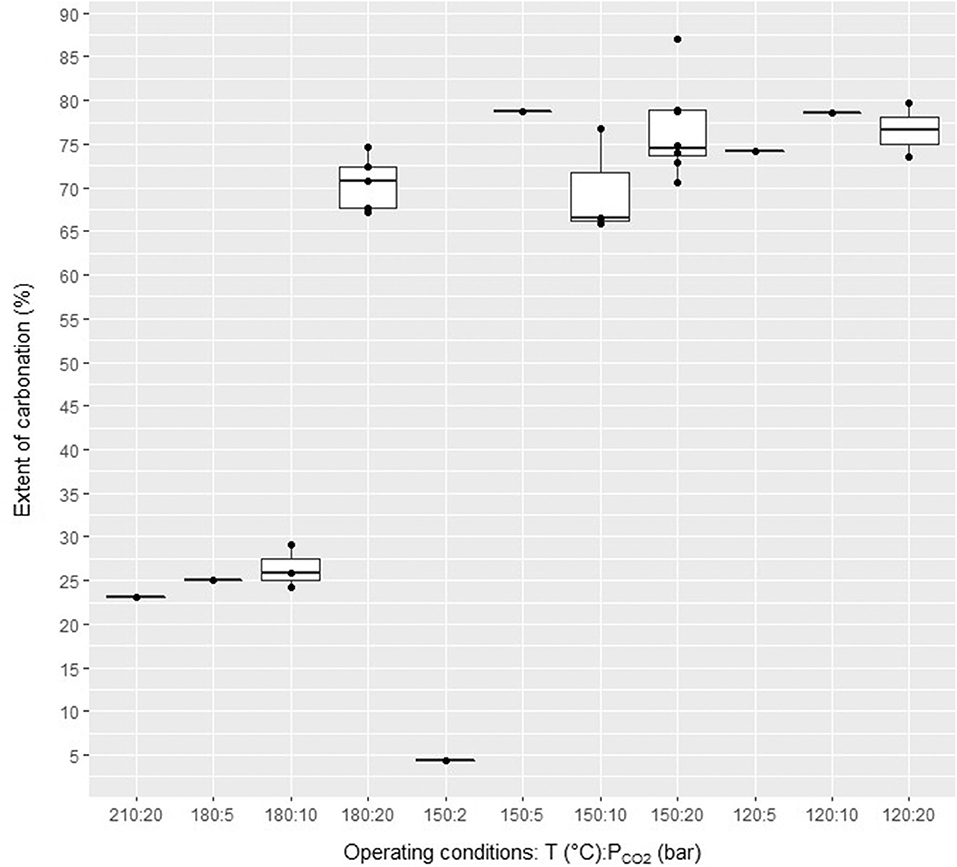
Figure 8. Measured extent of carbonation (27 observations in total) of the attrition-leaching carbonation process with ferronickel slag (reaction time = 24 h).
Figure 9A shows the statistical analysis of observations in the high performance range (carbonation extent > 60%) for 24 h measurements, where the solid line is the average distribution of 21 observations. The carbonation extent obtained after 24 h is 74.2 ± 9.2% at 95% confidence. Figure 9B shows the average and 95% confidence envelope of 21 carbonation kinetic curves for the favorable carbonation conditions of Figure 8. As with the carbonation extent measured at 24 h reaction time, carbonation kinetics are found to be rather insensitive to T and PCO2 under the operating conditions used with the attrition-leaching reactor.
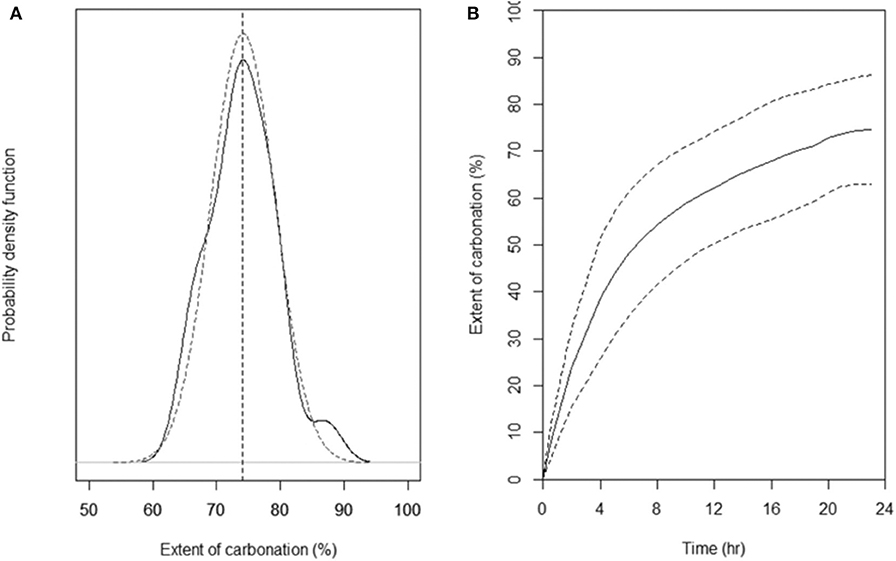
Figure 9. Statistical analysis (21 observations in total) of the measured extent and rate of carbonation for the favorable carbonation conditions of Ni-slags. (A) Measured (solid line) and fitted (dotted line) density distribution function of the extent of carbonation (B) Measured rate of carbonation (dotted lines give the 95% confidence interval).
The extent of carbonation measured after 24 h of reaction follows a normal distribution, as confirmed in Figure 9A. Analysis of the kinetic curves of 21 tests shows that distribution of carbonation extents at intermediate times is normal also. The quantification of the statistical distributions of the extent of carbonation as a function of reaction time is shown in Figure 10. This figure was obtained by fitting the normal distribution to all 21 kinetic curves at intermediate times, similarly to what was done in at 24 h in Figure 9A. This is precisely the information necessary for seeking solutions to the ICM inverse design problem, as inverse design problem solving requires that every system variable be characterized by a statistical distribution.
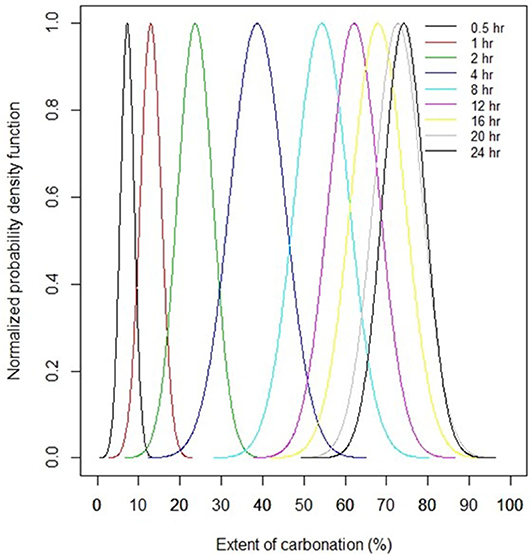
Figure 10. Statistical analysis of the variation of the extent of carbonation of Ni-slags as a function of reaction time (distributions move from left to right with increasing reaction time).
Not shown in the previous figures, one third of the observations were obtained at a solid concentration of 9 wt%, the other two thirds at 17 wt%. Within this solids concentration range, the carbonation extent and kinetics were unchanged. It remains to be verified whether this holds at higher solids concentration. High solids concentration testing however needs dispersants. The use of dispersants is standard practice in fine grinding to counter the increase in viscosity that results from the combination of elevated solid concentration and increasing particle fineness during attrition (Kapur et al., 1996). Incidentally, the chemical composition of grinding aids is a point of concern for ICM, as they may carry elements not allowed in construction materials, in the same way as minor elements contained in the feedstock. In this context, it is interesting to note that polyacrylates, commonly used as dispersants in ultrafine grinding, are also sometimes used as water reducing admixtures in the formulation of concrete.
The phases of carbonated products were characterized with the same techniques and protocol as earlier presented for ferronickel slag characterization. Techniques included XRD with quantitative Rietveld analysis using the external standard method (zincite), ICP-AES after total digestion, TGA (to measure the amount of CO2 after the carbonation process) and FTIR spectroscopy, as well as material balance on elements. As with the feedstock particles, analysis by XRD/Rietveld of carbonation products highlighted a high proportion of amorphous phase(s). Their characterization was carried out using FT-IR spectroscopy. A material balance confirmed the presence of amorphous hydrated silica and traces of a saponite type phase. The precise hydration state of both phases is difficult to obtain.
Figure 11A shows the average speciation of the phases before and after the attrition-leaching process, for the operating conditions that yield a high carbonation extent (see Figure 8). It is found that the carbonation process converts all the amorphous MgSi2O5 phase contained the ferronickel slag into hydrated amorphous silica and magnesite (MgCO3), according to Equation (1). As expected, the dissolution kinetics of forsterite is slower than that of amorphous MgSi2O5, so some unreacted forsterite is found in the carbonated product. The forsterite that has reacted is converted to magnesite, siderite (FeCO3) and amorphous silica (Equation 2). The siderite to magnesite molar ratio is equal to 0.1 and is the same as the iron to magnesium ratio in the native slag. The high Mg content of the feedstock leads to a high magnesite content of carbonation products, which is a challenge in terms of valorization.
The hydration rate of amorphous silica was estimated by considering that silica is the only hydrated phase in the carbonated slag (XRD patterns have shown that the carbonates are not hydrated) and that this phase loses its water during TGA analysis at a temperature below 100°C (Lin and Zhou, 2017).
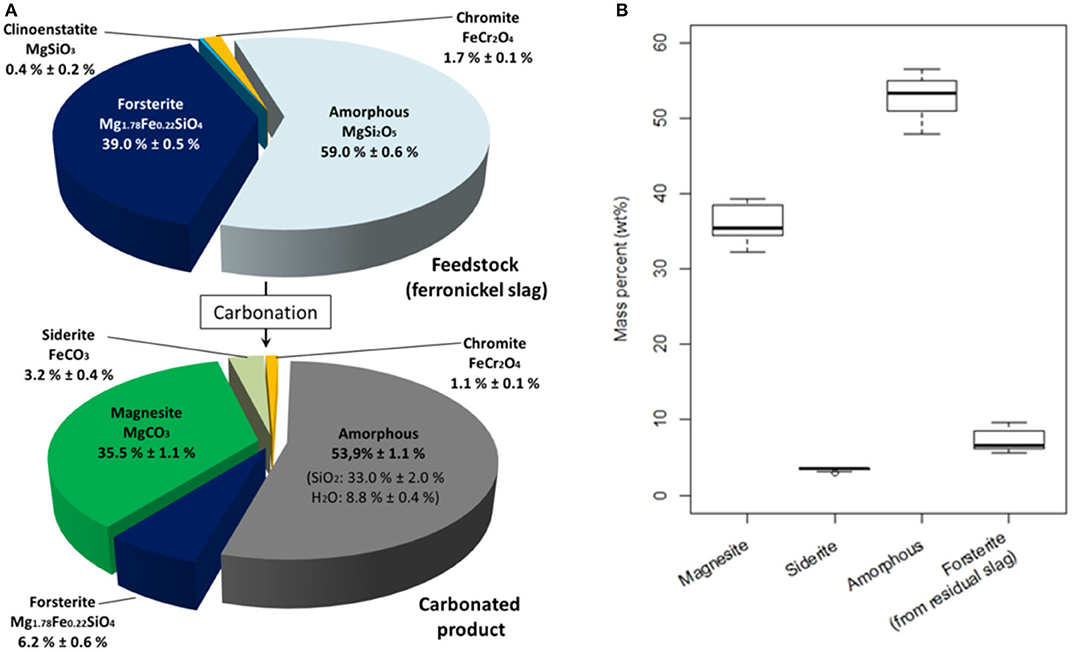
Figure 11. Mineralogical composition of feedstock (ferronickel slag) and carbonated products (A) Mineralogical speciation (wt%). (B) Mineralogical composition (15 observations) of carbonation products after 24 h of reaction.
The carbonation process also reduces the proportion of chromite in the carbonated product. Indeed, the chromite content is lower after carbonation due to the addition of water and carbon dioxide into the carbonated product.
The mineral composition of carbonated products also displays a composition that is stable over the operating conditions used. Figure 11B shows the mineralogical distribution of the carbonation products for all the test conditions for which carbonation extent exceeds 60% after 24 h of reaction. This invariance in composition of carbonated products under a wide range of operating conditions adds to the robustness of the attrition-leaching process for ICM of nickel slags.
With an aqueous mineral carbonation step, the transfer of products from the carbonation block to the valorization block requires a dewatering step. Carbonated particles have a PSD finer than 10 μm with specific gravity higher than 2.5. The continuous dewatering of this type of suspension is common in mining operations for fine ore and tailings processing, with centrifuges, vacuum filters and filter presses for instance. Thus, the search for industrial technological solutions to this problem does not seem to be problematic, even if one expects a high water content of the carbonated products after the dewatering stage. In the laboratory, a centrifuge operating at 11,200 rpm dewaters the carbonated products to between 35 and 55 wt% water in a few seconds. This produces a handlable material. Further testwork using a panel of dewatering technologies is necessary to model this dewatering stage, such that carbonated product moisture and energy consumption can be accounted for in the ICM inverse design problem.
The Valorization Block
One important issue is to identify the requirements of the final product considered, irrespective of the ICM pathway that may lead to producing the product in question. As a reminder, the example chosen in the article is the valorization of carbonated ferronickel slags as SCM for the manufacture of mortars.
Once the carbonated products have been characterized (mineralogy, particle size, moisture content), it is necessary to test them using SCM characterization methods, which will permit prediction of their behavior when used as SCM in mortars. Indeed, depending on their mineralogical composition, mineral additions will not exhibit the same properties (e.g., reactivity, water absorption) in a given cement medium, which will define their possible application scope. Typically, mineral additions are used to reduce the amount of clinker and/or improve the field performance of Portland cement based binders, mechanical or else (e.g., rheology or durability). With ICM, they have the additional advantage of making it possible to trap CO2 in construction materials, at the time of their making and additional to the CO2 that construction materials may capture over their lifetime.
Characterization of the type of mineral addition that can be obtained with carbonation products is the first step toward identifying possible valorization pathways as SCM. Indeed, there are three distinct types of mineral additions in calcium-silicate cements, namely hydraulic, pozzolanic, and inert additions (Kurdowski, 2014).
• Hydraulic additions have latent hydraulic properties; they react with water via hydration reactions to form other mineral phases after being activated by the high pH of the pore solution of the cement paste. This is the case for example with ground granulated blast furnace slags (GGBS), which can be used in cement manufacture with a substitution rate as high as 95%.
• Pozzolanic additions do not have intrinsic hydraulic properties. When in contact with lime and water they react to form hydrated calcium silicates. This is the case with siliceous materials such as silica fume or class F fly ash (siliceous fly ash) (Kurdowski, 2014). In France for instance, fly ash is allowed in concrete with a Portland cement substitution rate up to 30%, according to NF EN 206. The NF EN 197-1 standard, which is commonly used in New Caledonia, permits an even higher substitution rate if fly ash is used in cement manufacture to replace clinker. In some conditions and application, pozzolanic additions can improve the mechanical performance of structures over the long term, due to the formation of additional C-S-H as compared to standard binders with clinker only.
• Inert additions do not react in cement media, but make it possible to improve the compactness of the mixtures and serve as a nucleation support during hydration, which improves the overall mechanical performance.
The first test consisted in characterizing the reactivity of carbonated ferronickel slag in a calcium silicate cement medium. Reaction time is an issue here. For instance, the pozzolanic reaction is a slow reaction that appears only several days after the setting of the material, making it generally measurable only after 90 days in some cases, generally by mechanical testing. Here, the recently developed R3 test (Avet et al., 2016) was used as a first evaluation of carbonated slag reactivity, by creating a simplified medium that simulates the composition of the pore solution of an already partially hydrated binder. This test creates conditions favorable for the pozzolanic reactivity of SCMs. Despite the time gained to evaluate SCM reactivity, the R3 test alone cannot distinguish between pozzolanic and hydraulic reactivity. To this end, it needs to be coupled with a mineralogical analysis of mortars by XRD and by TGA, as well as by mechanical testing (measurement of compressive strength). To carry out the R3 test, the dewatered carbonated slag is first dried at 70°C for 24 h. Then, a paste is prepared by mixing carbonation products (SCM), lime (with a mass ratio lime/SCM = 3) and calcite (calcite/SCM = 0.5) powders in a solution that contains potassium hydroxide (0.07 mol.L−1) and potassium sulfate (0.23 mol.L−1) (Avet et al., 2016). The paste is then placed in an isothermal calorimeter at 40°C and the heat release is recorded as a function of time.
There are several accepted protocols in the literature for the R3 test, the most important point being the keep portlandite-to-SCM ratio and alkalinity the same (Snellings and Scrivener, 2016). In this work, the R3 test procedure was carried out using potassium sulfates and calcite as mixed powders, noting that the presence of limestone does not change the heat release in the R3 test (Avet et al., 2016). The R3 test results are shown in Figure 12 for carbonated and native ferronickel slag. It is noted that the carbonated product used here was produced by mixing together all the carbonation test products that had a carbonation yield of about 80%, irrespective of their test conditions since characterization has shown that they have the same composition. The curves represent the heat released during the reactions that take place in the paste over a 7-day period. With carbonated slag, it is significantly higher than with native slag. Lawrence et al. (2003) have found that the reactivity of SCM in cementitious medium depends on particle size, measuring a 23% increase in heat release with a hundredfold decrease in particle size (from 215 to 2 μm). Here, the particle size distribution of both native and carbonated slag differ by one order of magnitude. Indeed, native slag was dry milled and sieved at 100 μm prior to testing, whereas earlier measurements by Julcour et al. (2014) indicate that attrition-leached product have a 10 μm top size and a d50 around 5 μm after 24 h. The measured heat release increase of Figure 12 is greater than 400% for a 10-fold reduction in average particle size. This means that the measured difference in reactivity is not only due to the decrease in particle size but also to the chemical modifications between the native and carbonated slag. This finding is not surprising as the amorphous silica contained in carbonated slag is well-known to react with portlandite produced by cement hydration, making it a pozzolanic agent (Panesar, 2019). As the carbonated slag is reactive in a cement environment, it eliminates de facto the inert addition valorization pathway for carbonated ferronickel slag. For comparison sake, Table 2 gives the typical heat release for a selection of known SCMs (Avet et al., 2016). The reactivity of native slag is comparable to that of quartz, which is used as an inert addition in cements. Carbonated slags on the other hand have an extent of reactivity that is comparable with natural pozzolans.
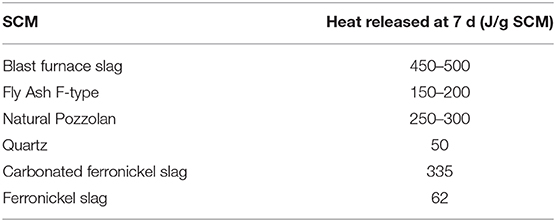
Table 2. Heat released during R3 test over a 7-day period (Avet et al., 2016).
Following the R3 test, the mineralogy of the 7-day-old paste containing the carbonated slag was characterized by TGA, in order to study the reactivity of portlandite during the test. This showed that the paste consumed 13 g of portlandite per g of SCM, which is of the same order of magnitude as that obtained with fly ash (Snellings and Scrivener, 2016). Therefore, it seems that carbonated ferronickel slag has a reactivity similar to pozzolans. Compressive strength measurement is still needed to conclude on the possible valorization pathways.
During these tests, we observed that carbonated slags absorbed a large amount of water since the fresh mortar with 20% of carbonated product seems very dry as compared with a standardized mortar. Since comparison of mechanical performance is done on an equal consistency basis, the consistency of mortars manufactured with carbonated slag had to be adjusted. This can be done either by adding water, at the risk of creating additional porosity in the final material, or by adding a water reducing agent (superplasticizer). In this work, the addition of a superplasticizer was favored in order to maintain a constant water-to-cement ratio. It could be noted that the superplasticizer could be made of the same molecule as the dispersant possibly used to increase the solids concentration in the attrition-leaching process. Such an additive could thus improve both the carbonation process and the consistency in fresh mortars.
Two mortars were prepared according to EN 196-1 standard: a reference mortar with 100% CEM I 52.5R cement and a mortar with 20% cement substituted by carbonated slag. It was necessary to add 1.3% of superplasticizer (CHRYSO®OPTIMA372) by mass in the mortar containing the carbonated slag in order to obtain the same consistency for both mortars, as measured using a mini slump test (17 cm after 15 punches on a punch table).
The compressive strength of 4 × 4 × 16 standardized samples was measured after 28 days of curing in sealed bags at 25°C for both mortars using a standardized 3R press (EN NF 196-1). With RSCM and RREF denoting respectively the compressive strength of the mortar with 20% carbonated slag and that of the reference mortar, compressive tests yielded RSCM= 56 MPa and RREF= 42 MPa. Therefore, replacing 20% of cement with carbonated nickel slag improves the mechanical behavior of mortars. The physical and chemical (i.e., pozzolanic) activities of the addition were evaluated using the strength activity index (Equation 3) (Bediako, 2018).
Here the strength activity index is equal to 134%. As a value of 100% means that 1 kg of cement can be replaced by 1 kg of SCM (and knowing that the carbonated slag contains amorphous silica), it was concluded here that the carbonated slag has a good pozzolanic activity and could be used as a pozzolanic addition at a replacement ratio of at least 20%.
To better understand the impact of this addition from a mineralogical standpoint, a TGA measurement was carried out at 28 days for both mortars. This is a standard test for measurement of portlandite content, since portlandite loses its water between 430 and 520°C (Villagrán-Zaccardi et al., 2017). Figure 13 shows that the portlandite content for the mortar made with carbonated slag is almost half that of the reference mortar. The actual values are 11.3 and 19.9% respectively. This decrease in portlandite content cannot be explained by the dilution alone (20% of cement was replaced by carbonated slag), so it is also considered as evidence of the pozzolanic reaction between the silica from the carbonated slag addition and the portlandite that results from the hydration of the cement paste.
Discussion
This section takes stock of what has been learned and what remains to be done for the complete characterization of the ICM technological pathway chosen in this article.
The previous section proposed a methodical exploration of the information necessary for the complete characterization of the elements of a particular ICM pathway, here that of the valorization of carbonated ferronickel slags as SCMs in mortar/concrete or as cement constituent. Even though it is one of the simplest possible valorization routes for carbonated nickel slag, the level of characterization work needed is already significant. Adding to this is the recognition that several aspects of SCM or cement constituent production cycle from nickel slags were not addressed in the paper, for the sake of brevity. It can therefore be concluded that characterization of ICM pathways requires a very substantial amount of testwork and analysis.
The selected feedstock, i.e., ferronickel slags cooled by quenching, was successfully characterized, and its compositional variability was found to be negligible over several years. With 3 Mt of slag being produced annually for a 140 year old industry, the abundance of the feedstock (current and projected reserves) is also a positive factor for the development of viable ICM pathways in the New-Caledonian context. The characteristics of the flue gas (flow rate, composition) emitted by the pyrometallurgical plant's thermal power station are also known and stable. These results and observations are globally favorable for development of ICM pathways in New-Caledonia. Other determining factors need to be considered as they relate to the feedstock block. One such factor is the energy used to grind the slag to reach the desirable PSD for the carbonation block.
The choice of carbonation technology weighs heavily on the characterization and performance of the carbonation block. One strong constraint of the selected ICM pathway is the use of the attrition-leaching mineral carbonation process operated inside a stirred media mill. The justification and assets of this mineral carbonation technology were amply discussed in the paper already. They are summarized hereafter:
• the intrinsic robustness of the attrition-leaching process to carbonate ferronickel slag across a wide range of temperature and CO2 partial pressure;
• the proven scalability of stirred media mills from liter to cubic meter scales;
• the advanced level of knowledge and models for stirred media mills (Ndimande et al., 2019);
• the industrial acceptability of stirred media mills.
As with the native slag, the carbonated slag was successfully characterized, and composition was found to be stable over a broad range of temperature and CO2 partial pressure. Carbonation extent and kinetics were measured with associated uncertainties. All the above results and observations lead to the conclusion that the carbonation block presents favorable attributes for the application of the ICM inverse design problem to the New-Caledonian ferronickel slag feedstock.
Additional testing and analysis is needed however in order to fully characterize the envelope of performance of the carbonation block, in particular as it relates to the operating conditions of the attrition-leaching reactor. This concerns the PSD of the feed slag, the nature, size and wear of the grinding media, the solids concentration of the suspension and the use of dispersant, the agitation speed, and of course, the energy consumption associated. The dewatering stage of carbonated products, which has received little attention thus far, is also an important system variable that requires dedicated experimental work for different eligible technologies.
Tests and analyses carried out to date have also confirmed that it is indeed possible to characterize all the elements of the valorization block of the ICM cycle. For the selected case study, which seeks to produce SCMs from carbonated ferronickel slags, dedicated reactivity tests have shown that carbonated slags cannot be considered as an inert addition. R3 test results, which will be completed by other reactivity tests, shows that carbonated ferronickel slags have a similar reactivity to natural pozzolans. Ongoing analysis, based on TGA and mechanical strength measurements, suggests that silica from the carbonated product reacts with portlandite to form calcium silicate hydrate (pozzolanic reaction) at 28 days of hydration.
To reach firm conclusions on the use of carbonated ferronickel slag as SCM or cement constituent, characterization on the scale of building materials must be carried out. Such tests include:
- Longer-term mechanical tests (90 and 180 days);
- Durability characterization of the material over time;
- Studies on the replacement ratio of cement/clinker by carbonated slag (here only 20% substitution was tested), for which it will be interesting to optimize the consistency of materials in the fresh state.
It is implicit that all additional tests required for commercialization of the carbonated slag as SCM or cement constituent on New-Caledonian and export markets would also be carried out.
Without sufficient quantities of carbonated slag, it is not possible to carry out the full range of tests required to fully characterize the use of carbonated slag as SCM or cement constituent. To fix ideas, manufacturing standardized mortars to perform EN-196-1 standard mechanical tests with a cement substitution of say 20% carbonated slag requires at least 100 grams of carbonated products. To carry out longer-term mechanical tests and with different substitution rates, it will be necessary to carry out several standardized mortars. Indeed, with a standardized mortar (EN 196-1), it is possible to prepare three 4 × 4 × 16 cm test pieces, requiring about 100 g of SCM. Measurement reproducibility further imposes to break 3 tests pieces (to have 6 compression strength values) per test condition (curing, age). In the end, it is necessary to have access to kilograms of carbonated slag in order to carry out standardized mechanical tests on 90 and 180 day mortars, whereas the carbonation reactor used in this study can provide ten of grams per test. A larger attrition-leaching reactor is currently being commissioned that will yield the desirable amount of carbonated slags.
The carbonated slag drying step at the interface between the carbonation block and the valorization block will also be the subject of particular attention for the selected pathway. In fact, until now, the slag is dried at 70°C in air after the dewatering step. However, even after drying, the materials carry ~3 wt% free water (characterized by TGA). It is being planned to study the effect of drying on the properties of carbonation products, mainly the reactivity of silica in a cement medium. The possibility of omitting this drying step altogether by adapting the amount of water when making mortar or concrete is also an avenue of research.
It is also important to take into consideration that the commercialization of new cementitious materials is not necessarily straightforward. In fact, this type of materials has to find their way on a market. With mineral additions, usual standards do not always apply (Vanderley et al., 2019). In fact, current standards require a specific composition for materials to be used as SCM or cement constituent, which does not include all of them. In particular, current standards do not include anything about using carbonated ferronickel slag as SCM or cement constituent. In addition, mortars are classified by strength for a fixed water-to-cement ratio, which does not take into account the water demand of these materials. For example, incorporating 20% of carbonated ferronickel slag as replacement for calcium silicate cement increases considerably the water demand of the paste, so that it is not possible to make a paste with a good consistency without adding water or a superplasticizer.
Conclusions
The proposed integrated CO2 mineralization (ICM) concept provides a conceptual framework for the development of viable carbon mineralization solutions in a given economic and societal context. ICM, whose boundaries extend from a material and CO2 feedstock to value-added products is pictured as a three concentric layer system: technological, industrial integration, and decision-making. As an early writing on the feasibility of the proposed ICM framework, the paper focuses on characterization of ICM's inner technological layer, within which technological pathways leading to given products are divided into three successive blocks: feedstock, carbonation, and valorization. With the view of finding viable ICM solutions, each conceivable technological pathway requires that all its constitutive elements be identified and characterized. As development of realistic ICM pathways on a given territory requires an iterative feedback process between systemic and technological scales, it is proposed that the search for viable ICM solutions be ultimately posed as an inverse design problem.
Exploration of ICM's technological layer is illustrated using a well-defined technological pathway, that of the valorization of ferronickel slags from New-Caledonia as supplementary cementitious material (SCM) or cement constituent. The regional context and the Mg-rich nature of the feedstock confer a significant value to this endeavor from a mineralization standpoint. Using attrition-leaching in a stirred media mill as the carbonation process, the experimental results presented in the paper confirm the feasibility of characterizing an ICM pathway fully. The work also recognizes that the study of integrated CO2 mineralization represents a leap in complexity and labor intensiveness compared to the sole development of efficient mineral carbonation processes. Considering the selected feedstock and regional context, the stability of the ferronickel slag feedstock and the robustness of the selected mineral carbonation attrition-leaching process are strong attributes in the face of ICM's intrinsic complexity.
It is recognized that the valorization block of the ICM cycle implies to work on a scale considerably larger than that used to study mineral carbonation processes. Indeed, one important teaching of this work on ICM is the need to move to a significant scale of production of carbonated materials in order to test the use properties of the final products. This observation has convinced the authors that a requisite of the development of ICM solutions is never to lose sight of the scalability of every individual steps along the ICM cycle. Adding to the urgency of climate change, this statement suggests that rapid development of large-scale ICM solutions should possibly favor unit operations and transformation processes whose validity on an industrial scale is proven. In no way does this pragmatic recommendation preclude the merits of seeking innovative processes, with improved carbonation kinetics and energy efficiency in particular.
Finally, it appears necessary to recontextualize the results that have been presented both in the overall ICM proposed framework and also in the context of the selected case study. What was established here, through a clearly defined example, is the feasibility of characterizing the individual components of a particular ICM technological pathway. It will not have escaped the reader that work remains to be done to fully characterize the selected technological pathway, even if the pending work does not affect the feasibility of the proposed approach. However, with the ferronickel slag feedstock from New-Caledonia, several marketable products can be envisioned, each product being associated with one specific technological pathway for its making. Characterization of all the components of ICM's inner technological layer, for a particular feedstock, requires that the work presented in this paper be repeated for every realistic pathway conceivable. Once this is accomplished, these pathways need to be linked to the industrial integration and decision-making layers of the proposed ICM framework. It is only then that solving the ICM system as an inverse design problem can be considered. While there is no obstacle in principle to apply the proposed ICM framework, the experimental and analysis work that is required to link all three ICM layers together is quite considerable. However, the authors hold the firm belief that this is a small price to pay considering the stakes associated with deployment of viable ICM solutions in a given economic and societal setting.
Data Availability Statement
All datasets generated for this study are included in the article/supplementary material.
Author Contributions
FB and PL wrote the first draft of the manuscript, which was revised, read, and approved by all authors.
Conflict of Interest
The authors declare that the research was conducted in the absence of any commercial or financial relationships that could be construed as a potential conflict of interest.
Acknowledgments
This work is part of an ongoing multi-disciplinary research effort co-funded by the New Caledonian Energy Agency ACE (grant #CS17-3160-00) and the French Environment and Energy Management Agency ADEME (grant #1894C0021). It brings together different research institutes with the combined expertise required to develop the proposed ICM concepts to New-Caledonian nickel slag: LGC (lgc.cnrs.fr) on carbonation technology development, LMDC (www-lmdc.insa-toulouse.fr) on alternative building materials design, Université Gustave Eiffel (www.ifsttar.fr), LEMNA (lemna.univ-nantes.fr), and ESO (eso-nantes.cnrs.fr) on environmental, societal and economic assessment, BRGM (www.brgm.fr) on industrial integration, and CNRT (cnrt.nc) on regional coordination in New-Caledonia.
References
Ashraf, W., and Olek, J. (2016). Carbonation behavior of hydraulic and non-hydraulic calcium silicates: potential of utilizing low-lime calcium silicates in cement-based materials. J. Mater. Sci. 51, 6173–6191. doi: 10.1007/s10853-016-9909-4
Atakan, V., Sahu, S., Quinn, S., Hu, X., and DeCristofaro, N. (2014). Why CO2 matters – advances in a new class of cement. ZKG 67, 60–63.
Avet, F., Snellings, R., Alujas Diaz, A., Ben Haha, M., and Scrivener, K. (2016). Development of a new rapid, relevant and reliable (R3) test method to evaluate the pozzolanic reactivity of calcined kaolinitic clays. Cement Concrete Res. 85, 1–11. doi: 10.1016/j.cemconres.2016.02.015
Azdarpour, A., Asadullah, M., Junin, R., Manan, H., Hamidi, H., and Daud, A. R. M. (2014). Carbon dioxide mineral carbonation through ph-swing process: a review. Energy Proc. 61, 2783–2786. doi: 10.1016/j.egypro.2014.12.311
Bediako, M. (2018). Pozzolanic potentials and hydration behavior of ground waste clay brick obtained from clamp-firing technology. Case Stud. Constr. Mater. 8, 1–17. doi: 10.1016/j.cscm.2017.11.003
Bodénan, F., Bourgeois, F., Petiot, C., Augé, T., Bonfils, B., Julcour, C., et al. (2014). Ex-situ mineral carbonation for CO2 mitigation: evaluation of mining waste resources, aqueous carbonation processability and life cycle analysis (Carmex project). Miner. Eng. 59, 52–63. doi: 10.1016/j.mineng.2014.01.011
Bonfils, B., Julcour, C., Guyot, F., Chiquet, P., Bodenan, F., and Bourgeois, F. (2012). Feasibility of direct aqueous mineral carbonation using dissolution enhancing organic additives. Int. J. Greenhouse Gas Control 9, 334–346. doi: 10.1016/j.ijggc.2012.05.009
Bourgeois, F., Julcour-Lebigue, C., Cassayre, L., Bailly, F., Cyr, M., and Touzé, S. (2018). “Guiding mineralization process development with geochemical modelling,” in 14th Greenhouse Gas Control Technologies Conference, (GHGT-14) (Melbourne, VIC).
Bowen, N. L., and Anderson, O. (1914). The binary system: MgO-SiO2. Am. J. Sci. 37, 487–500. doi: 10.2475/ajs.s4-37.222.487
Bukowski, J. M., and Berger, R. L. (1979). Reactivity and strength development of CO2 activated non-hydraulic calcium silicates. Cement Concrete Res. 9, 57–68. doi: 10.1016/0008-8846(79)90095-4
Cassayre, L., Bourgeois, F., Julcour-Lebigue, C., Benhamed, I., Diouani, J., and Nahdi, K. (2016). “Defining the operating conditions of the attrition-leaching process using thermodynamic process modelling,” in Proceedings of the International Mineral Processing Congress IMPC 2016: XXVII (Québec, QC).
Comminution Handbook (2015). “Chapter 8 – Stirred Mills,” in Spectrum Series 21, ed A. Lynch (Australasian Institute of Mining and Metallurgy), 324. Available online at: https://ausimm.com/product/comminution-handbook-pdf/
Damen, K., Faaij, A., van Bergen, F., Gale, J., and Lysen, E. (2005). Identification of early opportunities for CO2 sequestration—worldwide screening for CO2-EOR and CO2-ECBM projects. Energy 30, 1931–1952. doi: 10.1016/j.energy.2004.10.002
Dlugogorski, B. Z., and Balucan, R. D. (2014). Dehydroxylation of serpentine minerals: implications for mineral carbonation. Renew. Sustain. Energy Rev. 31, 353–367. doi: 10.1016/j.rser.2013.11.002
Eden, M. R., Jorgensen, S. B., Gani, R., and El-Halwagi, M. M. (2004). A novel framework for simultaneous separation process and product design. Chem. Eng. Process. 43, 595–608. doi: 10.1016/j.cep.2003.03.002
Farnam, Y., Villani, C., Washington, T., Spence, M., Jain, J., and Weiss, W. J. (2016). Performance of carbonated calcium silicate based cement pastes and mortars exposed to NaCl and MgCl2 deicing salt. Constr. Build. Mater. 111, 63–71. doi: 10.1016/j.conbuildmat.2016.02.098
Faruque, M. M., Baliban, R. C., Elia, J. A., and Floudas, C. A. (2012a). Modeling, simulation, and optimization of postcombustion CO2 capture for variable feed concentration and flow rate. 1. Chemical absorption and membrane processes. Indus. Eng. Chem. Res. 51, 15642–15664. doi: 10.1021/ie301571d
Faruque, M. M., Baliban, R. C., Elia, J. A., and Floudas, C. A. (2012b). Modeling, simulation, and optimization of postcombustion CO2 capture for variable feed concentration and flow rate. 2. Pressure swing adsorption and vacuum swing adsorption processes. Indus. Eng. Chem. Res. 51, 15665–15682. doi: 10.1021/ie301572n
Favier, A., De Wolf, C., Scrivener, K., and Habert, G. (2018). A Sustainable Future for the European Cement and Concrete Industry - Technology Assessment for Full Decarbonisation of the Industry by 2050. Zürich: ETH, 96. doi: 10.3929/ethz-b-000301843
Gao, M., Young, M. F., Cronin, B., and Harbort, G. (2001). IsaMill medium competency and its effect on milling performance. Miner. Metallurg. Process. 18, 117–120. doi: 10.1007/BF03402882
Gartner, E. (2017). “CSA- and belite-rich clinkers and cements,” in Symposium the Future of Cement – 200 Years After Louis Vicat (Paris).
International Energy Agency (2016). 20 Years of Carbon Capture and Storage - Accelerating Future Deployment. OECD/IEA.
Jankovic, A., Valery, W., and La Rosa, D. (2003). “Fine grinding in the Australian mining industry,” in Proceedings of the 3rd International Conference on Recent Advances in Materials, Minerals and Environment (RAMM 2003).
Joint Research Centre (2011). “Recommendations for life cycle impact assessment in the European context,” in International Reference Life Cycle Data System (ILCD) Handbook. Luxembourg: European Commission. Available online: http://eplca.jrc.ec.europa.eu/uploads/ILCD-Handbook-LCIA-Background-analysis-online-12March2010.pdf.
Julcour, C., Bourgeois, F., Bonfils, B., Benhamed, I., Guyot, F., Bodénan, F., et al. (2014). Development of an attrition-leaching hybrid process for direct aqueous mineral carbonation. Chem. Eng. J. 262, 716–726. doi: 10.1016/j.cej.2014.10.031
Kapur, P. C., Healy, T. W., Scales, P. J., Boger, D. V., and Wilson, D. (1996). Role of dispersants in kinetics and energetics of stirred ball mill grinding. Int. J. Miner. Process. 47, 141–152. doi: 10.1016/0301-7516(96)00003-8
Krevor, S. C., and Lackner, K. S. (2011). Enhancing serpentine dissolution kinetics for mineral carbon dioxide sequestration. Int. J. Greenhouse Gas Control 5, 1073–1080. doi: 10.1016/j.ijggc.2011.01.006
Kulkami, N., Khan, D., Gupta, R., Gautham, B.p, Allen, J. K., Panchal, J., et al. (2014). “Inverse design of manufacturing process chains,” in Proceedings of the ASME 2014 International Design Engineering Technical Conferences & Computers and Information in Engineering Conference IDETC/CIE 2014 (Buffalo, NY).
Kurdowski, W. (2014). “Mineral additions for cement production,” in Cement and Concrete Chemistry (Dordretch: Springer), 533–583. doi: 10.1007/978-94-007-7945-7_7
Lawrence, P., Cyr, M., and Ringot, E. (2003). Mineral admixtures in mortars Effect of inert materials on short-term hydration. Cement Concrete Res. 33, 1939–1947. doi: 10.1016/S0008-8846(03)00183-2
Lin, B., and Zhou, S. (2017). Poly(ethylene glycol)-grafted silica nanoparticles for highly hydrophilic acrylic-based polyurethane coatings. Prog. Org. Coat. 106, 145–154. doi: 10.1016/j.porgcoat.2017.02.008
Mission Innovation (2018). Accelerating Breakthrough Innovation in Carbon Capture, Utilization, and Storage. Report of the Carbon Capture, Utilization and Storage Experts' Workshop (Houston, TX).
National Petroleum Council (2019). “Chapter Nine – CO2 use,” in Meeting the dual challenge – A Roadmap to At-Scale Deployment of Carbon Capture, Use and Storage. Library of Congress Control Number: 2020931901.
Ndimande, C. B., Cleary, P. W., Mainza, A. N., and Sinnott, M. D. (2019). Using two-way coupled DEM-SPH to model an industrial scale stirred media detritor. Miner. Eng. 137, 259–276. doi: 10.1016/j.mineng.2019.03.001
Panesar, D. K. (2019). “3 - Supplementary cementing materials,” in Woodhead Publishing Series in Civil and Structural Engineering, Developments in the Formulation and Reinforcement of Concrete (Second Edition), ed S. Mindess (Woodhead Publishing), 55–85. doi: 10.1016/B978-0-08-102616-8.00003-4
Picot, J. C., Cassard, D., Maldan, F., Greffié, C., and Bodenan, F. (2011). Worldwide potential for ex-situ mineral carbonation. Energy Proc. 4, 2971–2977. doi: 10.1016/j.egypro.2011.02.206
Power, I. M., Harrison, H. L., Dipple, G. M., Wilson, S. A., Kelemen, P. B., Hitch, M., et al. (2013). Carbon mineralization: from natural analogues to engineered systems. Rev. Miner. Geochem. 77, 305–360. doi: 10.2138/rmg.2013.77.9
Rim, G., Wang, D., Rayson, M., Brent, G., and Park, A. H. (2020). Investigation on abrasion versus fragmentation of the si-rich passivation layer for enhanced carbon mineralization via CO2 partial pressure swing. Indus. Eng. Chem. Res. 59, 6517–6531. doi: 10.1021/acs.iecr.9b07050
Sanna, A., Uibu, M., Caramanna, G., Kuusik, R., and Maroto-Valer, M. M. (2014). A review of mineral carbonation technologies to sequester CO2. Chem. Soc. Rev. 43, 8049–8080. doi: 10.1039/C4CS00035H
Schneider, M. (2019). The cement industry on the way to a low-carbon future. Cement Concrete Res. 124:105792. doi: 10.1016/j.cemconres.2019.105792
Schneider, M., Romer, M., Tschudin, M., and Bolio, H. (2011). Sustainable cement production – present and future. Cement Concrete Res. 41, 642–650. doi: 10.1016/j.cemconres.2011.03.019
Snellings, R., and Scrivener, K. L. (2016). Rapid screening tests for supplementary cementitious materials: past and future. Mater. Struct. 49, 3265–3279. doi: 10.1617/s11527-015-0718-z
Spinelli, M., Martínez, I., De Lena, E., Cinti, G., Hornberger, M., Spörl, R., et al. (2017). Integration of Ca-looping systems for CO2 capture in cement plants. Energy Proc. 114, 6206–6214. doi: 10.1016/j.egypro.2017.03.1758
Umemoto, K. (2017). Phase transitions in MgSiO3 post-perovskite in super-Earth mantles. Earth Planet. Sci. Lett. 478, 40–45. doi: 10.1016/j.epsl.2017.08.032
Vanderley, M. J., Quattrone, M., Abrão, P., and Cardoso, F. A. (2019). Rethinking cement standards: opportunities for a better future. Cement Concrete Res. 124:105832. doi: 10.1016/j.cemconres.2019.105832
Ventura, A., and Antheaume, N. (2019). “Environmental assessment of carbon capture and utilization: a new systemic vision – Application to valorization of nickel slags,” in Proceedings of the International Workshop CO2 Storage in Concrete – CO2STO2019 (Marne La Vallée: IFSTTAR).
Villagrán-Zaccardi, Y. A., Egüez-Alava, H., De Buysser, K., Gruyaert, E., and De Belie, N. (2017). Calibrated quantitative thermogravimetric analysis for the determination of portlandite and calcite content in hydrated cementitious systems. Mater. Struct. 50, 179. doi: 10.1617/s11527-017-1046-2
Winnefeld, F., Epifania, E., Montagnaro, F., and Gartner, E. M. (2019). “New insights into the hydration of cementitious materials based on magnesium carbonates,” in 1st International Conference on Innovation in Low Carbon Cement and Concrete Technology (London).
Keywords: CO2 utilization, mineralization, construction materials, supplementary cementitious materials, waste valorization, ferronickel slag
Citation: Bourgeois F, Laniesse P, Cyr M and Julcour C (2020) Definition and Exploration of the Integrated CO2 Mineralization Technological Cycle. Front. Energy Res. 8:113. doi: 10.3389/fenrg.2020.00113
Received: 16 March 2020; Accepted: 12 May 2020;
Published: 09 June 2020.
Edited by:
Rafael Mattos Dos Santos, University of Guelph, CanadaReviewed by:
Guy Mercier, Institut National de la Recherche Scientifique (INRS), CanadaCaleb Michael Woodall, Worcester Polytechnic Institute, United States
Alastair T. M. Marsh, University of Leeds, United Kingdom
Copyright © 2020 Bourgeois, Laniesse, Cyr and Julcour. This is an open-access article distributed under the terms of the Creative Commons Attribution License (CC BY). The use, distribution or reproduction in other forums is permitted, provided the original author(s) and the copyright owner(s) are credited and that the original publication in this journal is cited, in accordance with accepted academic practice. No use, distribution or reproduction is permitted which does not comply with these terms.
*Correspondence: Florent Bourgeois, florent.bourgeois@toulouse-inp.fr